
A novel approach of evaluating crushing energy in ball
1. Introduction. Ball mill is a kind of widely used engineering machinery with low working efficiency [1, 2].Since the advent of the ball mill, researches on its grinding performance mainly aimed at the aspects of fill rate, rotational speed, ratio of steel balls, Ball Mill an overview ScienceDirect Topics,Conical Ball Mills differ in mill body construction, which is composed of two cones and a short cylindrical part located between them (Fig. 2.12).Such a ball mill body is expedient Failure analysis of a ball mill located in a cement’s ,The ball mill understudy has a length of 13.07 m in its cylindrical geometry and a length between supports of 16.2 m (Fig. 1a,b).The formation of cracks in the

Ball Mill Grinding Theory Crushing
The object of these tests was to determine the crushing efficiency of the ballmill when crushing in closed circuit with a classifier. Ball Mill Parameter Selection & Calculation JXSC,1 Calculation of ball mill capacity. The production capacity of the ball mill is determined by the amount of material required to be ground, and it must have a certain Ball Charge and Grinding Efficiency Grinding,Efficiency is in part determined by the Axb value of the ore. A small lab mill can give guidance on the influence of ore strength and ball size. Larger balls will increase P80 in ball mill, thereby reducing
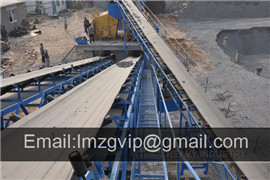
Why use Different Size Balls in a Mill
In test 3, in which the grid was used to segregate the different sizes of balls, a further advantage of about 4 percent in efficiency is shown. The conical mill in test 4 increased the efficiency to 58 percent Ball Mill Balls Grinding Medium used in the Ball Mill for ,Ball Mill Balls. Ball Mill Balls is the grinding medium of ball mill equipment. The effect of grinding and peeling is produced by the collision and friction between the Factors Affecting Ball Mill Grinding Efficiency,The following are factors that have been investigated and applied in conventional ball milling in order to maximize grinding efficiency: a) Mill Geometry and Speed Bond (1954) observed grinding efficiency

Value Of Crushing Strength Of Balls In Ball Mill
Ball Mill_MECRU. 31 The use of highstrength and wearresistant combined hammer head can save materials and reduce waste. 3. The working principle of the ball mill is Advances in Mechanical Engineering , Vol. 13(3) 1–9 ,The mill speed is one of the vital parameters in ball mills, which is normally specified as a fraction of critical speed. It determines whether the load behavior is predominantly the cascading regime, the cataracting regime or the centrifuging regime. In general, the industrial ball mills rotational speed operates at 70%~80% of criticalGrain size and shape fractal characteristics of gangue in ,(2) Ball Mill; The model of the ball mill used in this test is SMφ500×500mm test mill,the grinding medium is steel balls, the maximum single charge is 5 Kg, the maximum load of the grinding body is 100 Kg, the power is 1.5 kw, and the speed is 48 rpm. Rolling bearings mainly support the working principle, and the cylinder is driven to

Ball Mill Explained saVRee
For both wet and dry ball mills, the ball mill is charged to approximately 33% with balls (range 3045%). Pulp (crushed ore and water) fills another 15% of the drum’s volume so that the total volume of the drum is 50% charged. Pulp is usually 75% solid (crushed ore) and 25% water; pulp is also known as ‘ slurry ’.Ball Mills Mineral Processing & Metallurgy,CERAMIC LINED BALL MILL. Ball Mills can be supplied with either ceramic or rubber linings for wet or dry grinding, for continuous or batch type operation, in sizes from 15″ x 21″ to 8′ x 12′. High density Numerical investigation on particle mixing in a ball mill,Mixing behavior of particles is an essential process for a ball mill. In order to investigate particle mixing, a three dimensional model was established for particle dynamics in a ball mill. Firstly, the Discrete Element Model was adopted to track each particle in the ball mill. which finally fluctuated around the unique value periodically
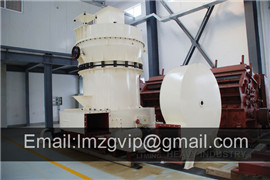
Ball Milling Metallurgist & Mineral Processing
The use of ball mills for reducing crusher product to 85 per cent,: below 200mesh in two stages, as practised at the United Eastern, Tom Reed, and Montana mines, in Arizona, is a distinct advance in fine The Ultimate Guide to Ball Mills miningpedia.net,The Grinding Media Of Ball Mill Steel Balls back to top. The steel balls in ball mill are consumable, which need to be supplied from now and on. 1. The filling rate of steel balls. Steel balls undertake the main job in grinding, therefore, the number of steel balls in ball mill is highly relative with the grinding strength.Why use Different Size Balls in a Mill,In test 3, in which the grid was used to segregate the different sizes of balls, a further advantage of about 4 percent in efficiency is shown. The conical mill in test 4 increased the efficiency to 58 percent

Technical methods of activating minerals by crushing
Activation by Crushing, Fracture of elasticbrittle solids (the category to which most minerals belong) In particular, it may occur under repeated forces well below the breaking strength. This type of fracture, known as cold hardening or metal fatigue, is well known, and appears, e.g., in chipping or peeling of metal scales in antifriction`Grinding Aid Effectiveness in Cement Ball Mill,Download Free PDF. Grinding Aid Effectiveness in Cement Ball Mill Web: bulawali Email: bulawali@gmail, ali@bulawali LinkedIn: Ali Bulawali Date: Sep of grinding balls (Grinding Media) ranging from 2 cm to 90 cm or 100 cm diameter, in addition to large surface area for different sizes of grinding Balls the grinded substanceGrain size and shape fractal characteristics of gangue in ,(2) Ball Mill; The model of the ball mill used in this test is SMφ500×500mm test mill,the grinding medium is steel balls, the maximum single charge is 5 Kg, the maximum load of the grinding body is 100 Kg, the power is 1.5 kw, and the speed is 48 rpm. Rolling bearings mainly support the working principle, and the cylinder is driven to
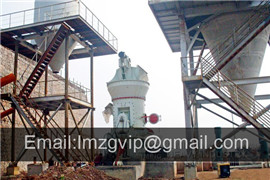
Ball Mill Explained saVRee
For both wet and dry ball mills, the ball mill is charged to approximately 33% with balls (range 3045%). Pulp (crushed ore and water) fills another 15% of the drum’s volume so that the total volume of the drum is 50% charged. Pulp is usually 75% solid (crushed ore) and 25% water; pulp is also known as ‘ slurry ’.Numerical investigation on particle mixing in a ball mill,Mixing behavior of particles is an essential process for a ball mill. In order to investigate particle mixing, a three dimensional model was established for particle dynamics in a ball mill. Firstly, the Discrete Element Model was adopted to track each particle in the ball mill. which finally fluctuated around the unique value periodicallyBall Mill Ball Mills Wet & Dry Grinding DOVE,DOVE small Ball Mills designed for laboratories ball milling process are supplied in 4 models, capacity range of (200g/h1000 g/h). For small to large scale operations, DOVE Ball Mills are supplied in 17 models, capacity range of (0.3 TPH 80 TPH). With over 50 years experience in Grinding Mill Machine fabrication, DOVE Ball Mills as

Choose the Best Grinding Steel Balls for Your
Medium balls: 80mm. Large steel balls: 100mm or 120mm. Super large balls: 130mm to 150mm. Theoretically, when the filling amount of steel grinding balls in the cylinder of the ball mill is 40%, the ball mill The Ultimate Guide to Ball Mills miningpedia.net,The Grinding Media Of Ball Mill Steel Balls back to top. The steel balls in ball mill are consumable, which need to be supplied from now and on. 1. The filling rate of steel balls. Steel balls undertake the main job in grinding, therefore, the number of steel balls in ball mill is highly relative with the grinding strength.Technical methods of activating minerals by crushing,Activation by Crushing, Fracture of elasticbrittle solids (the category to which most minerals belong) In particular, it may occur under repeated forces well below the breaking strength. This type of fracture, known as cold hardening or metal fatigue, is well known, and appears, e.g., in chipping or peeling of metal scales in antifriction

`Grinding Aid Effectiveness in Cement Ball Mill
Download Free PDF. Grinding Aid Effectiveness in Cement Ball Mill Web: bulawali Email: bulawali@gmail, ali@bulawali LinkedIn: Ali Bulawali Date: Sep of grinding balls (Grinding Media) ranging from 2 cm to 90 cm or 100 cm diameter, in addition to large surface area for different sizes of grinding Balls the grinded substanceHow to choose between ball mill and vertical roller mill?,The vertical mill has high grinding efficiency and low energy consumption, and the power consumption is only 40%50% of the ball mill. 7. Finished product quality. Compared with the ball mill, the product of the vertical mill has a higher degree of homogenization and higher purity.Cement Ball Mill JXSC Machine,The cement ball mill is mainly used for grinding the finished products and raw materials of cement plants, and is also suitable for grinding various ore and other grindable materials in industrial and