
Choosing the right primary crusher for your aggregate
The first step in choosing a primary crusher takes place at a high level. It’s necessary to identify the purpose the crusher will be used for. This purpose is a given What Type of Crusher Is Best for Primary ,Similar to Sizers, Roll Crushers can be used for the primary crushing of soft to medium hard material that can be slightly abrasive, dry, or wet and sticky. They are typically used in heavy mining Primary Crusher Selection & Design Mineral ,Dependability and long service life are landmarks of good primary crusher design of up to 30 yrs. The selection of the primary
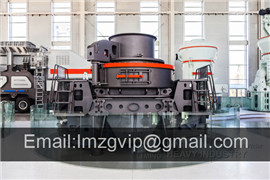
What is a Primary Crusher? machinerypartner
A primary crusher breaks up large pieces of rock or concrete from the blasting or excavation process and turns them into smaller, more manageable chunks. This is the first step in Primary crusher Designs and costs archmiko.cz,primary crusher designs and costs . Crusher selection guide — CrushologyA crusher is a major investment so it's essential to select one with the potential to meet your needs into primary crusher designs and costs diseno de chancadora pdf,Primary Crusher Designs And Costs Vetura Mining Machinery Primary Crusher Designs And Costs; Primary Crusher Designs And Costs . A gyratory crusher can b [email
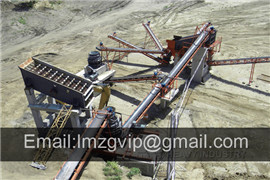
primary crusher designs and costs Exomos
primary crusher designs and costs Kredyty Prywatne Od primary crusher designs and costsusa.primary crusher designs and costsusa Limestonecrusherplant in Primary Crusher Designs And Costs wyspaskopelos.pl,Primary Crusher Designs And Costs. Capital Cost Direct Costs. The largest primary gyratory crushers cost US 2 million or more, while overall crushing plant Industrial Solutions Gyratory crushers ThyssenKrupp,designed for high performance and, at the same time, costeffective operation, i.e. low servicing and maintenance costs. When it comes to crushing blasted hard rock in ore and natural stone mining, the efficiency of thyssenkrupp gyratory crushers in primary crushing is second to none. KB 6389 for iron ore.

Primary Impact Crushers MEKA Crushing
MEKA’s primary impact crusher liners are designed to be interchangeable, meaning less inventory space is needed and reduced inventory cost for our customers. The blow bars are also designed to be reversible for the Impact Crushers Primary McLanahan,McLanahan offers a wide selection of Impact Crushers for quarried limestone and semiabrasive minerals. McLanahan draws from the 75 years of field experience with the Universal line of Impactors, which includes impact breakers and Andreasstyle impactors. At present, we offer the New Hollandstyle primary impact breaker and the MaxCap X Types of Crushers: What You Need to Know Machinery ,Hammer Mills and Impact crushers: One of the most versatile crushers available, hammer mills and impactors can be primary, secondary, and tertiary crushers. Hammer crushers use continuous hammer blows to shatter and disintegrate material. They are typically horizontal rotating in an enclosed cylinder casing.
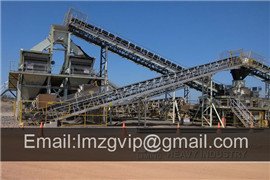
Selecting the right type of crushing equipment
The most important characteristics of a primary crusher include the capacity and ability to accept raw material without blockages. A large primary crusher is more expensive to purchase than a smaller Primary Crushing Mineral Processing,The term “primary crusher,” by definition, might embrace any type and size of crushing machine. The term implies that at least two stages of crushing are involved, but in many cases the machine which Crushing and Screening AggNet,The impact crusher is one of the most versatile crusher types available and offers the advantages of high reduction ratio with lower horsepower per ton. Hammermill (primary) Typically, hammermills are used for soft, nonabrasive and dry materials, although some ‘nonclog’ models can accommodate wet or sticky materials.
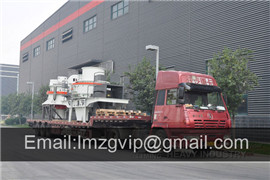
Modelling of crushing operations in the aggregates
Figure 14: JKSimMet screen shot. Data on the power draw and crusher energy is entered. 31 Figure 15: JKSimMet screen shot. Comparison of plant and JKSimMet generated data. 32 Figure 16: Diagram to illustrate decking in blastholes. 36 Figure 17: Cross section of a gyratory crusher. 40 Figure 18: Cross section of a jaw crusher. 40Material Selection for Crusher Jaw in a Jaw ,primary operations are comminution and co ncentration. adopted for various designs (Chan and Zhou, 199 4 and . Dieter, 1991). 2. that maximizes performanc e and minimizes cost for crusher .primary crusher designs and costs Exomos,primary crusher designs and costs Kredyty Prywatne Od primary crusher designs and costsusa.primary crusher designs and costsusa Limestonecrusherplant in usLimestoneCrusherwith Reasonable Pricecrusheris a crushing machine which is mainly used to process all kinds of limestones. Besides this limestone.
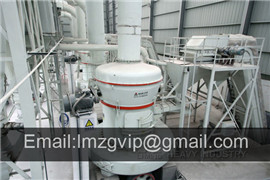
Industrial Solutions Gyratory crushers ThyssenKrupp
designed for high performance and, at the same time, costeffective operation, i.e. low servicing and maintenance costs. When it comes to crushing blasted hard rock in ore and natural stone mining, the efficiency of thyssenkrupp gyratory crushers in primary crushing is second to none. KB 6389 for iron ore.Cost Analysis for Crushing and Screening Part II CORE,Cost Analysis for Crushing and Screening Part II started to produce a simple and transportable jaw‐crusher for farmers to produce gravel for the earlier dirt roads. 2014 resulted in developing of a primary model to be used to estimate/predict the cost for a single crushed product within a simple crushing/comminutionCrushers QueensMineDesignWiki,Operating Costs. The primary operating costs of a crusher are parts and labour for maintenance, which can vary approximately twice as much as the power for the motor. Gyratory crushers generally cost
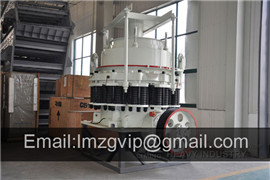
What is a Primary Crusher? machinerypartner
A primary crusher breaks up large pieces of rock or concrete from the blasting or excavation process and turns them into smaller, more manageable chunks. This is the first step in the crushing process. The smaller pieces can then either be prescreened or fed directly into a secondary impact or cone crusher.Selecting the right crusher for your operations,Best suited for secondary crushing applications, cone crushers are designed to crush presized materials, usually 100mm, 150mm or 200mm, depending on the size of the crusher. Cone crushers can HE Parts Brochure Crusher Liners,Similarly, increasing primary crusher tonnage at the expense of crushed product size is likely to have a negative effect on SAG mill performance. HE Parts range of 1418% manganese steels that provide a lowcost option for applications where wear rates are relatively low or Extended chamber gyratory and jaw crusher designs. Full

Crushing and Screening AggNet
The impact crusher is one of the most versatile crusher types available and offers the advantages of high reduction ratio with lower horsepower per ton. Hammermill (primary) Typically, hammermills are used for soft, nonabrasive and dry materials, although some ‘nonclog’ models can accommodate wet or sticky materials. Crusher Plant Crusher Prices Crusher for Sale Fabo,It continues to offer original solutions to its customers with its very low maintenance costs, innovative designs and 19 years of experience. FABO within the scope of mobile stone crushing plants can be listed as follows: DMK03 impact crusher or PDK120 primary impact crusher can be given as examples.Modelling of crushing operations in the aggregates ,Figure 14: JKSimMet screen shot. Data on the power draw and crusher energy is entered. 31 Figure 15: JKSimMet screen shot. Comparison of plant and JKSimMet generated data. 32 Figure 16: Diagram to illustrate decking in blastholes. 36 Figure 17: Cross section of a gyratory crusher. 40 Figure 18: Cross section of a jaw crusher. 40
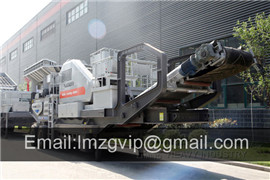
Material Selection for Crusher Jaw in a Jaw
primary operations are comminution and co ncentration. adopted for various designs (Chan and Zhou, 199 4 and . Dieter, 1991). 2. that maximizes performanc e and minimizes cost for crusher .,,