
Coal Mill an overview ScienceDirect Topics
ObserverBased and Regression ModelBased Detection of Emerging Faults in Coal Mills. Peter Fogh Odgaard, Sten Bay Jørgensen, in Fault Detection, Supervision and Safety of Technical Processes 2006, 2007. 5.2 Experiments with and design of the regression COAL MILL Land Instruments International,in the coal mills. While appropriate precautions differ at the various stages of the process, this article concentrates on appropriate detection methods for coal mills. CDC Mining Best Practices for Dust Control in Coal ,Mining Publication: Best Practices for Dust Control in Coal Mining. Second edition. The extraction, transport, and processing of coal produces respirablesized dust
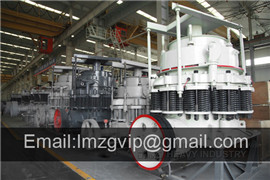
Analysis of International Best Practices for Coal Mine
desired or optimum result.” To a certain extent, the concept of “best practice” can be understood as “best policy measures” or (in a broader context) “best Details Home Parker Hannifin,Coal mill dust collectors have a substantial effect on productivity, yet have received relatively little attention as companies implement costsaving programs, like the Madhya Pradesh,Operational Support Features for Mill Maintenance 25 vi. Practices To Prevent Barring Gear Stalling 26 vii. Practices On Hydrogen Leakage Problem 27 viii.
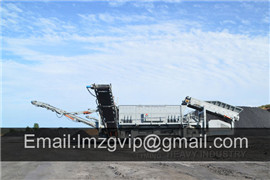
Coal Mill Coal Mill In Cement Plant AGICO Cement
The coal mill grinding system is an important part of the dry process cement manufacturing. In cement plants, we usually adopt the air swept coal mill system or vertical mill system best practices in coal mill maintenance Grinding Mill China,PRB COAL USERS’ GROUP (PRBCUG). to determine the best practices for coal mill inerting and fire suppression in maintenance issues that tend to render the system’s best practices in coal mill maintenance Exomos,best practicesofcoal mill maintenance magazene.nl.best practices in coal mill maintenance pochirajucoin. FlexibleCoal: Evolution from Baseload to Peaking Plant,NREL

Subcommittee Members Canadian Institute of Mining,
Coal Subcommittee Members Don MillsFording Coal Colin McKennyFording Coal Geoff JordanNorwest Gary Johnston Luscar Coal Dave Hughes Coal Mill an overview ScienceDirect Topics,ObserverBased and Regression ModelBased Detection of Emerging Faults in Coal Mills. Peter Fogh Odgaard, Sten Bay Jørgensen, in Fault Detection, Supervision and Safety of Technical Processes 2006, 2007. 5.2 Experiments with and design of the regression modelbased approach. Operating data from a coal mill is used to compare the fault detection In discussion Vincent Grosskopf, Coal Mill Safety Global ,01 February . Vincent Grosskopf has more than 45 years of experience in bulk material handling, particularly regarding the safety of coal grinding systems. As the founder of Coal Mill Safety, he acts as a consultant to those seeking to design and build safe greenfield coal grinding systems or improve existing installations.
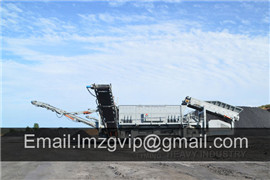
Coal Drying Improves Performance and Reduces
causes less feeder hopper bridging and plugging problems. Coal feeders provide coal to the coal pulverizers (mills) where the coal is pulverized and dried. Dryer coal is easier to pulverize, and less mill power is needed to achieve the same coal fineness. Additionally, with less fuel moisture, more complete drying of coal can be achieved in the Madhya Pradesh,Operational Support Features for Mill Maintenance 25 vi. Practices To Prevent Barring Gear Stalling 26 vii. Practices On Hydrogen Leakage Problem 27 viii. Best Practices For Electrical Failure Reduction 28 ix. Arrangements For Overhaul Of Units 30 x. Practices In Chemical Treatment 34 • Coal Mills Sieve Analysis • DGA for GeneratorPulverizer Plant O&M Aspects,NomenclatureBowl Mills 583 XRS / 803 XRP Bowl mills 58,80 stands for bowl diameter in inches If the number is even then its shallow bowl mill. If the number is odd then its deep bowl mill 3 number of rollers three nos. X frequency of power supply 50 cycles.In USA ’x’ means 60 cycles. R Raymond, name of the inventor
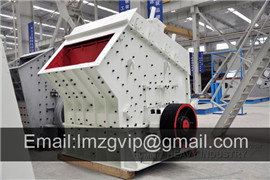
Power Plant Maintenance: A Complete Guide Flyability
The Elios 2 conducting an inspection at a coalfired power plant in the Ukraine. 4. Prolonging Asset Lifespans. Because drone inspections are so much more costeffective than manual inspections, drones allow companies to increase the frequency of inspections while still realizing significant savings.. Over time, increasing the frequency of Mill Inerting Systems Presentation to the ASBCUG,Coal Mills are the Heart of a Coal Fired Plant. Maximum capacity, reliability and performance of your operation rely on the critical roles that your coal mills perform: Conditioning coal for proper combustion. (Fineness, fuel distribution, throughput) Delivering 100% of fuel to the boiler. Profoundly influencing ability to generate powerCoal Mill in Cement Plant Vertical Roller Mill & AirSwept ,The most used coal mills in cement plants are airswept ball mills and vertical roller mills. At present, most cement plants use coal as the main fuel in the clinker production process. The standard coal consumed by the new dry process for producing 1 ton of cement clinker is usually between 100 kg and 130 kg, and the fuel cost accounts for
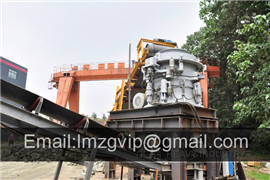
Coal Silo Fires and Hot Spots: Extinguishing and
Please contact clientservices@accessintel or call 8887075814 (M Th 9 am 5:30 pm and F 9 am 3 pm. ET),to start a free trial, get pricing information, order a reprint, or post anbest practices in coal mill maintenance Exomos,best practicesofcoal mill maintenance magazene.nl.best practices in coal mill maintenance pochirajucoin. FlexibleCoal: Evolution from Baseload to Peaking Plant,NREL modifications to operationalpractice, however, an increase in strategicmaintenancecan minimize the impact on outage,plant and operating systems that enabled thecoalplant,Coal Mill an overview ScienceDirect Topics,ObserverBased and Regression ModelBased Detection of Emerging Faults in Coal Mills. Peter Fogh Odgaard, Sten Bay Jørgensen, in Fault Detection, Supervision and Safety of Technical Processes 2006, 2007. 5.2 Experiments with and design of the regression modelbased approach. Operating data from a coal mill is used to compare the fault detection

A unified thermomechanical model for coal mill operation
Lee (1986) proposed a model in which all important processes occurring inside the mills are modeled based on the fundamental physical laws. Coal particles are divided into nine discrete sizes. Drag force, momentum, and energy conservation equations are combined to compute the pressure drop and temperature profiles.Coal Drying Improves Performance and Reduces ,causes less feeder hopper bridging and plugging problems. Coal feeders provide coal to the coal pulverizers (mills) where the coal is pulverized and dried. Dryer coal is easier to pulverize, and less mill power is needed to achieve the same coal fineness. Additionally, with less fuel moisture, more complete drying of coal can be achieved in theCurrent State, Strategy for the Future unece,Workshop on Best Practices in Coal Mine Methane Capture and Utilisation 10 June , TKI, Ankara TURKISH COAL MINING SECTOR Current State, Strategy for the Future . OUTLINE Mücella Ersoy, CMM Workshop,10 June , Ankara . Overview of Mining Sector in Turkey

Best Practices in Underground Coal Gasification Semantic
Optical Properties of Coal after ExSitu Experimental Simulation of Underground Gasification at Pressures of 10 and 40 bar. Coal gasification experiments were carried out in a reactor used to simulate underground coal gasification (UCG) processes under ex situ conditions at pressures of 10 and 40 bar. Changes in the.Coal Mill Safety,VG: At best, coal mill safety is not well understood and, at worst, it is ignored. When it comes to coal mill systems, most cement plant operators just presume that the supplier of the equipment knows all of the Sample preparation for coal analysis Romquest,important step to take before analysing coal is sample preparation with laboratory crushers and mills to obtain a representative sample. For more inhomogeneous coal samples, such as brown coal, the sample preparation step becomes even more important in ensuring reproducible analysis results. The fineness of the sample can

Pulverizer Plant O&M Aspects
NomenclatureBowl Mills 583 XRS / 803 XRP Bowl mills 58,80 stands for bowl diameter in inches If the number is even then its shallow bowl mill. If the number is odd then its deep bowl mill 3 number of rollers three nos. X frequency of power supply 50 cycles.In USA ’x’ means 60 cycles. R Raymond, name of the inventor Madhya Pradesh,Operational Support Features for Mill Maintenance 25 vi. Practices To Prevent Barring Gear Stalling 26 vii. Practices On Hydrogen Leakage Problem 27 viii. Best Practices For Electrical Failure Reduction 28 ix. Arrangements For Overhaul Of Units 30 x. Practices In Chemical Treatment 34 • Coal Mills Sieve Analysis • DGA for GeneratorCoal Mill in Cement Plant Vertical Roller Mill & AirSwept ,The most used coal mills in cement plants are airswept ball mills and vertical roller mills. At present, most cement plants use coal as the main fuel in the clinker production process. The standard coal consumed by the new dry process for producing 1 ton of cement clinker is usually between 100 kg and 130 kg, and the fuel cost accounts for