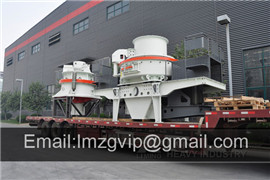
Cement grinding optimisation ScienceDirect
making cement by the chemical reaction between the components of the ground mixture. This chemical reaction occurs at high temperature in a rotary kiln, grinding the cement clinker nodules to 100% passing 90 μm in a dry circuit. Grinding occurs at the (PDF) Clinker grinding process and cement properties,Abstract. Sustainability of cement products is increased by reducing grinding energy and limiting CO2 emissions. Cement additives permit to reach bothe the Application of Intellectual Control Treatment for Cement ,Cement grinding process play an important role in cement industrial production, which affects the quality and various performance indicators of the cement directly [1].Using
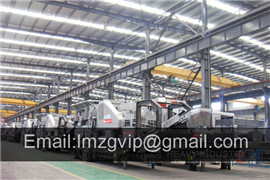
Cement Production Process Cement Manufacturing
In general, a full cement production process includes the stone crushing, raw mill process, clinker process, and cement grinding process, cement packing process, (PDF) Simulation of Cement Grinding Process for Optimal ,Abstract. The control of cement grinding/mixing process in an industrial mill regarding SO3 content has been effectively simulated taking into account all its Cement Manufacturing Process: 6 StepsTo Make ,During the cement grinding process, when the clinker is ground to a fine powder with other raw materials, up to 5% gypsum or additional anhydrite is added to control the solidification time of the
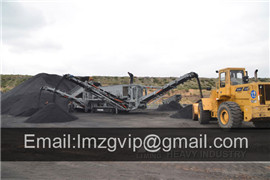
Cement Grinding Unit Cement Grinding Plant Cement
The process of cement grinding station can be divided into three types: opencircuit grinding system, closedcircuit grinding system, and combined grinding Cement Manufacturing Process Phases Flow ,Cement Manufacturing Process Phase 1: Raw Material Extraction. Cement uses raw materials that cover calcium, silicon, iron and aluminum. Such raw materials are limestone, clay and sand. Limestone Ball Mill & Roller Press Systems for Cement Grinding ,The cement pregrinding system. The most noticeable feature of the roller press cement pregrinding system is that the fine material power ground at the middle part of the roller will

Cement Manufacturing Process HeidelbergCement India
Cement is packed by high efficiency rotary packers which are electronically controlled. Packers are highly precise with tolerance of +/ 0.5%. The main feature of electronic Cement grinding optimisation ScienceDirect,The current world consumption of cement is about 1.5 billion tonnes per annum and it is increasing at about 1% per annum. The electrical energy consumed in cement production is approximately 110. kWh/tonne, and around 40% of this energy is consumed for clinker grinding.. There is potential to optimise conventional cement clinker Cement Grinding Mineral Processing,A typical raw mix consists of 7585% limestone, 1225% shale, the balance consisting of silica or quartzite and iron oxide. Exact proportioning is dependent upon their chemical properties before and
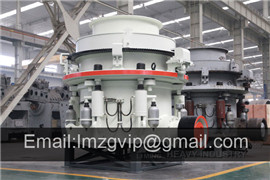
Characterisation and management of concrete grinding
Concrete grinding residue is the waste product resulting from the grinding, cutting, and resurfacing of concrete pavement. Potential beneficial applications for concrete grinding residue include use as a soil amendment and as a construction material, including as an additive to Portland cement concrete. Concrete grinding residue exhibits a high(PDF) Simulation of Cement Grinding Process for Optimal ,The control of cement grinding/mixing process in an industrial mill regarding SO3 content has been effectively simulated taking into account all its fundamental sides and particularities. Based onBest Concrete Grinders ( Reviews ) ToolsPros,If you’re not sure what features make a reliable concrete grinder, you can check out the buying guide at the end of the article. And if you want a comparison between the best options available, check them out below. The 6 Best Concrete Grinders for 1. DeWalt DWE46153 Angle Grinder Best Budget Concrete Grinder
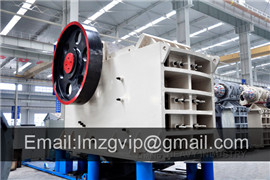
Cement Extraction and processing Britannica
There are four stages in the manufacture of portland cement: (1) crushing and grinding the raw materials, (2) blending the materials in the correct proportions, (3) burning the prepared mix in a kiln, and (4) grinding the burned product, known as “ clinker,” together with some 5 percent of gypsum (to control the time of set of the cement). The three processes of 500 TPD standalone cement grinding unit at Dheevanur ,Sakthipriyan Cements. Environmental clearance is sought for the proposed 500 TPD standalone cement grinding unit for manufacturing of ordinary portland cement (OPC), pozzolanic portland cement (PPC), and portland slag cements (PSC) at Dheevanur village, Thindivanam, Villuppuram District, Tamil Nadu.Cement Production Process AGICO,Cement grinding: The clinker is taken from the clinker silo and sent to the feed bin where it is mixed with gypsum and additives before entering the cement grinding plant. In the cement grinding process, the clinker is ground to a fine powder along with other materials, up to 5% gypsum or additional anhydrite is added to control the

PROCESS CONTROL FOR CEMENT GRINDING IN
The process variables in cement grinding process using VRM are strongly nonlinear and having large time delay characteristics also dynamics changes within 24 minutes. The fast dynamics necessitate closer attention to the process condition and taking corrective action in time. In this paper, the various conventional and modern control Cement Grinding Process Explanations liajones 博客园,Cement ball mill, also names cement mill, cement clinker mill, is the important equipment for grinding cement clinker, gypsum, limestone, clay, coal immediately after crushing procedure. This really is basically a big rotating drum containing grinding media generally steel balls.PROCESS CONTROL FOR CEMENT GRINDING IN ,The process variables in cement grinding process using VRM are strongly nonlinear and having large time delay characteristics also dynamics changes within 24 minutes. The fast dynamics necessitate closer attention to the process condition and taking corrective action in time. In this paper, the various conventional and modern control

Overview of cement grinding: fundamentals, additives,
Grinding is an essential operation in cement production given that it permits to obtain fine powder which reacts quickly with water, sets in few hours and hardens over a period of weeks. i11.6 Portland Cement Manufacturing US EPA,11.6 Portland Cement Manufacturing 11.6.1 Process Description17 Portland cement is a fine powder, gray or white in color, that consists of a mixture of accomplished during grinding in ballandtube mills or roller mills. While thermal energy for drying can be supplied by exhaust gases from separate, directfired coal, oil, or gas Cement Manufacturing Process Phases Flow ,Cement Manufacturing Process Phase II: Proportioning, Blending & Grinding. The raw materials from quarry are now routed in plant laboratory where, they are analyzed and proper proportioning of
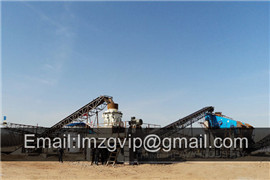
Cement Grinding Cement Plant Optimization
Cement grinding operation may be performed in one of the following mill setups. Ball and tube mills. Vertical Roller Mills (VRM). Roller press with Ball mill. Ball Mill. Ball mills with high efficiency separators have been used for cement grinding in cement plants all these years. Ball mill is a cylinder rotating at about 7080% of criticalCement Grinding Process Explanations_weixin_30433075的,Cement ball mill, also names cement mill, cement clinker mill, is the important equipment for grinding cement clinker, gypsum, limestone, clay, coal immediately after crushing procedure. This really is basically a big rotating drum containing grinding media generally steel balls.Cement Grinding Mineral Processing,A typical raw mix consists of 7585% limestone, 1225% shale, the balance consisting of silica or quartzite and iron oxide. Exact proportioning is dependent upon their chemical properties before and
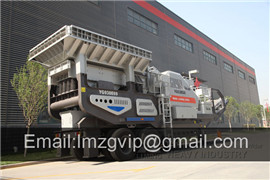
How to Choose the Right Concrete Grinding
Some of the higherquality walkbehind concrete floor grinders have a grinding width of 21 inches, while others can grind a 32inch section of your floor in a single pass. Handheld grinders are used in tighter spaces, such Grinding Aids at Best Price in India IndiaMART,Cement Grinding Aid (STEMOL CGA 4010) ₹ 87,000/ PIECE Get Latest Price. Country of Origin: Made in India. 4010 prevents cement particles from reagglomeration or readhering, during and after the grind ing process 500 TPD standalone cement grinding unit at Dheevanur ,Sakthipriyan Cements. Environmental clearance is sought for the proposed 500 TPD standalone cement grinding unit for manufacturing of ordinary portland cement (OPC), pozzolanic portland cement (PPC), and portland slag cements (PSC) at Dheevanur village, Thindivanam, Villuppuram District, Tamil Nadu.