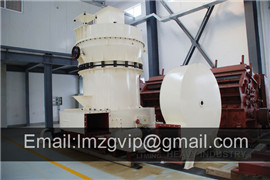
Fruitful design specifiions crushing circuit rock quarry
Contribute to changjiangsx/Fruitful development by creating an account on GitHub.Crushing & Screening Plant Design Factors Mineral ,Crushing Plant Design and Layout ConsiderationsCrushing Circuit “A’’ shows a small simple layout for use in mills up to 100 tons. In order to keep the flowsheet Selection oof Comminution Circuits for Improved Efficiency,ores to simplify the crushing circuit and improve power efficiency. The cost of HPGRs biases there effective use to large tonnage circuits, with 60 t/h units costing
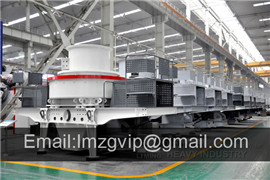
Crushing & Grinding Circuit Design
By definition “work index is the power required to comminute a short ton of a material from an Crushing Plant Flowsheet & Design ,Crushing Plant Flowsheet & DesignLayout. In the crushing section, the ore as it comes from the mine is broken down dry to a size suitable for the wet grinding Evaluating the Impacts of Jaw Crusher Design ,primary crushing stage to 10–20 cm [1], [2]. The process of size reduction is normally designed to take place in single stage open circuit, single stage closed circuit
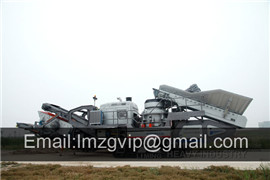
(PDF) Design and Development of Plastic Crusher for a
The efficiency of crushing based on polymers processed are 90% for HDPE, 68% for LDPE, 45% for PVC and 10% for PET bottles. The developed crusher (PDF) Mechanical System Design ResearchGate,Besides, CATIA is used for part analysis which is kinematic analysis. This project is mainly about designing and analyzing duo operating can crusher by using the UVM项目自学笔记之一:阅读design specification,将IC验证的整个流程划分为如下阶段,并按照流程完成整个项目:. 1.阅读design specification,目的:. (1)学习设计的架构:包括整个soc架构,待验的IP架构.

Crushing Circuit an overview ScienceDirect Topics
The first step of physical beneficiation is crushing and grinding the iron ore to its liberation size, the maximum size where individual particles of gangue are separated from the iron minerals. A flow sheet of a typical iron ore crushing and grinding circuit is shown in Figure 1.2.2 (based on Ref. [4]).This type of flow sheet is usually followed when the crude ore Three ways to improve your crushing circuit for increased ,Optimize. There are a couple of steps to optimizing a crushing circuit– firstly to optimize machine performance, and secondly to optimize the overall performance of your circuit. Optimizing a machine involves verifying all aspects of your equipment to maximize process and mechanical performance. The crusher’s chamber is a good place Perfecting the Performance of Secondary Crushers E & MJ,Ideally, the deck on the scalping screen should have a cut point equal to the closed side setting (CSS) of the crusher. The feed size to a secondary crusher is typically in the range of 50 mm to 250 mm (up to 300 mm). If the capacity is higher, the acceptable feed size gets larger. After crushing, the product is in the range of 060 mm (75 mm
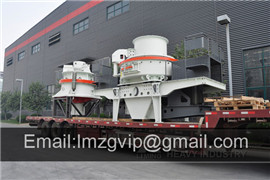
(PDF) Modelling and simulation of
PDF On Apr 1, 2013, Gauti Asbjörnsson and others published Modelling and simulation of dynamic crushing plant behavior with MATLAB/Simulink Find, Optimizing Performance of SABC ,This research is focused on the Phase I SABC milling circuit of the Wushan porphyry copper mine. Improvements to the existing circuit were targeted without DEVELOPMENT OF A PROTOTYPE ,There are three main steps to design a suitable crushing plant, (1) proces s design, (2) equipment selection, and (3) layout. The first and second steps are
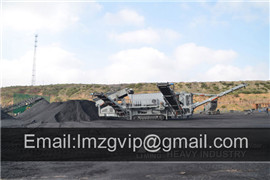
COMMINUTION CIRCUIT OPTIMISATION
Changes to crushing and stockpile management. Cyclone reconfiguration. Control philosophy and System implementation. Ramped up production from a 250 tph base to 450 tph in a 6 month period. [6] Geita (2010) Changes to control and operating philosophy. Modifications to crushing circuit and cyclones. Greatly increased circuit Impact of plant upgrade and DMS on the processing ,common opencircuit secondary crusher (H8800600kW) ahead of the ROM stockpile would improve the crushing plant delivery rate and the performance of the tertiary crushing circuit. A decision was also made to upgrade the flotation circuit on a prorata basis, in order to treat the higher process flows.CMOS Circuit Design, Layout, and Simulation, 3rd Edition,图书CMOS Circuit Design, Layout, and Simulation, 3rd Edition 介绍、书评、论坛及推荐 登录/ 注册 下载豆瓣客户端 豆瓣 6.0 全新发布 × 豆瓣 扫码直接下载 iPhone · Android 豆瓣 读书 电影 音乐 同城 小组 阅读 FM 时间 豆品 豆瓣读书 搜索: 购书单 电子图书
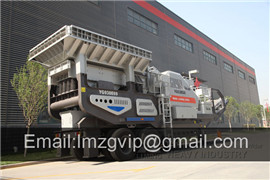
CMOS VLSI Design (豆瓣)
内容简介 · · · · · ·. For both introductory and advanced courses in VLSI design, this authoritative, comprehensive textbook is highly accessible to beginners, yet offers unparalleled breadth and depth for more experienced readers. The Fourth Edition of CMOS VLSI Design: A Circuits and Systems perspective presents broad and indepthPerfecting the Performance of Secondary Crushers E & MJ,Ideally, the deck on the scalping screen should have a cut point equal to the closed side setting (CSS) of the crusher. The feed size to a secondary crusher is typically in the range of 50 mm to 250 mm (up to 300 mm). If the capacity is higher, the acceptable feed size gets larger. After crushing, the product is in the range of 060 mm (75 mmMineral Crushing and Grinding ,Mineral Crushing and Grinding Circuits: Their Simulation, Optimisation, Design and Control . by . A. J. Lynch (Author) › Visit Amazon's A. J. Lynch Page. Find all
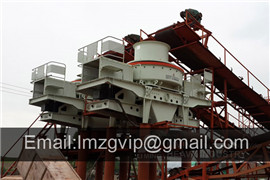
Introduction to Mineral Processing Sepro Labs
3.2.1 Crushing Equipment Primary Crushers Jaw and Gyratory Within the crushing circuit, a primary crusher reduces material down to a size that can be conveyed and fed to the secondary crushing circuit. The two most common primary crushers used for coarse runofmine material are the jaw and gyratory crushers.A review of modeling and control strategies for cone ,a tertiary crushing circuit typically goes through several more comminution and concentration steps until the valuable mineral is liberated from the raw ore. For this reason, state of the art cone crusher control technology in the mineral processing industry seems to be lagging; the crushing stage is overlooked because it is only a part of aEvaluating the Impacts of Jaw Crusher Design ,primary crushing stage to 10–20 cm [1], [2]. The process of size reduction is normally designed to take place in single stage open circuit, single stage closed circuit or multiple stage open or closed circuit. In some cases a combination of these methods are adopted. In a single stage, single pass, open circuit size

COMMINUTION CIRCUIT OPTIMISATION
Changes to crushing and stockpile management. Cyclone reconfiguration. Control philosophy and System implementation. Ramped up production from a 250 tph base to 450 tph in a 6 month period. [6] Geita (2010) Changes to control and operating philosophy. Modifications to crushing circuit and cyclones. Greatly increased circuit Pedro Ferreira Pinto and Homero Delboni Júnior,circuits developed are: a crushing and ball mill circuit (CB), a SAG mill and ball mill circuit (SAB), and a single stage SAG mill circuit (SSSAG). For the SAB circuit, the use of pebble crushing is analyzed, SAB/C route. Figure 1 shows the grinding circuits studied in this work. Figure 1 Grinding Circuits. For each circuit, the energy conImpact of plant upgrade and DMS on the processing ,common opencircuit secondary crusher (H8800600kW) ahead of the ROM stockpile would improve the crushing plant delivery rate and the performance of the tertiary crushing circuit. A decision was also made to upgrade the flotation circuit on a prorata basis, in order to treat the higher process flows.
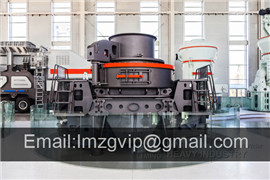
Gold extraction
Comminution is the process where ore particles are liberated from gangue material through progressive size reduction in the form of crushing, Crushing Plant Design and Layout ,1 Considerations of stone crusher plant design. The basic purpose of crushing ore is to achieve a certain particle size requirement for ore, raw materials or fuel. In ore dressing, ,