
Ball Mill an overview ScienceDirect Topics
Conical Ball Mills differ in mill body construction, which is composed of two cones and a short cylindrical part located between them (Fig. 2.12).Such a ball mill body is expedient because efficiency is appreciably increased. Peripheral velocity along the conical drum Ball Mill Loading Dry Milling Paul ,The starting point for ball mill media and solids charging generally starts as follows: 50% media charge; Assuming 26% void space between spherical balls (nonspherical, Converting a ball mill from overflow to grate discharge,If a mill has available power, conversion of the discharge arrangement from overflow to grate can be beneficial in allowing increased throughput or a finer

Ball Charge and Grinding Efficiency
Ball mill grind is based on different principle; it has some attributes similar to SAG mill Ball Mill an overview ScienceDirect Topics,8.3.2.2 Ball mills. The ball mill is a tumbling mill that uses steel balls as the grinding media. The length of the cylindrical shell is usually 1–1.5 times the shell diameter (Figure 8.11 ). Ball Mills Mineral Processing,CERAMIC LINED BALL MILL. Ball Mills can be supplied with either ceramic or rubber linings for wet or dry grinding, for continuous or batch type operation, in

Optimization of the makeup ball
Abstract and Figures. The combination of a grinding circuit simulator with a model of ball wear in a grinding mill leads to a method to calculate, with a Ball Mill Charge Grinding & Classification Circuits,The ball charge and ore charge volume is a variable, subject to what is the target for that operation. The type of mill also is a factor as if it is an overflow mill (subject Ball Mill Parameter Selection & Calculation JXSC,1 Calculation of ball mill capacity. The production capacity of the ball mill is determined by the amount of material required to be ground, and it must have a certain

cement mill fine ball charge.md at main · dinglei/en
Contribute to dinglei/en development by creating an account on GitHub.Ball Mill RETSCH powerful grinding and homogenization,RETSCH is the world leading manufacturer of laboratory ball mills and offers the perfect product for each application. The High Energy Ball Mill E max and MM 500 were developed for grinding with the highest energy input. The innovative design of both, the mills and the grinding jars, allows for continuous grinding down to the nano range in the shortest Converting a ball mill from overflow to grate discharge,If a mill has available power, conversion of the discharge arrangement from overflow to grate can be beneficial in allowing increased throughput or a finer product size. Conversely, if the mill does not have available power then it is still possible to install a grate discharge and to draw the same power by using a lower ball charge.
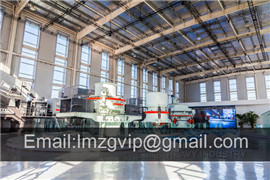
Ball Mill Explained saVRee
For both wet and dry ball mills, the ball mill is charged to approximately 33% with balls (range 3045%). Pulp (crushed ore and water) fills another 15% of the drum’s volume so that the total volume of the drum is 50% charged. Pulp is usually 75% solid (crushed ore) and 25% water; pulp is also known as ‘ slurry ’.Ball Charge and Grinding Efficiency,Ball mill grind is based on different principle; it has some attributes similar to SAG mill optimization. SAG mill breaks with stirring the kidney at optimized kidney specific AMIT 135: Lesson 7 Ball Mills,Mill Type Overview. Three types of mill design are common. The Overflow Discharge mill is best suited for fine grinding to 75 106 microns.; The Diaphram or Grate Discharge mill
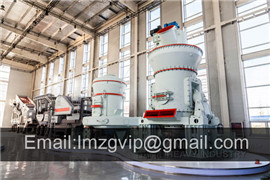
Retsch : 粉碎设备 : 球磨仪 : PM 400
行星式球磨仪 PM 400. The PM 400 is a robust floor model with 4 grinding stations and accepts grinding jars with a nominal volume from 12 ml to 500 ml. It processes up to 8 samples simultaneously which results in a high sample throughput. The extremely high centrifugal forces of Planetary Ball Mills result in very high pulverization energyTUMBLING MILL MECHANICS,A tumbling mill is a collective name for the generally known ball mills, rod mills, tube mills, pebble mills and autogeneous mills. For all these kinds of displays a fine grinding effect too: affected by the mill shell the individual balls will rotate (Fig. 12/5); this effect is brought about by the friction to the of the mill chargeGrinding in Ball Mills: Modeling and Process Control,Keywords: Ball mills, grinding circuit, process control. I. Introduction Grinding in ball mills is an important technological process applied to reduce the size of particles which may have different nature and a wide diversity of physical, mechanical and chemical characteristics. Typical examples are the various ores, minerals, limestone, etc.
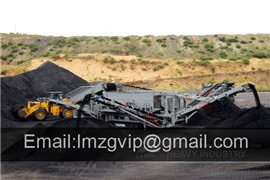
Checking your browser Pharmapproach
The balls which could be of different diameter occupy 30 50 % of the mill volume and its size depends on the feed and mill size. The large balls tend to break down the coarse feed materials and the smaller balls help to form fine product by reducing void spaces between the balls. Ball mills grind material by impact and attrition.cement mill fine ball charge.md at main · dinglei/en,Contribute to dinglei/en development by creating an account on GitHub.MODULE #5: FUNCTIONAL PERFOMANCE OF BALL ,If a ball mill contained only coarse particles, then 100% of the mill grinding volume and power draw would be applied to the grinding of coarse particles. In reality, the mill always contains fines: these fines are present in the ball mill feed and are produced as the particles pass through the mill.
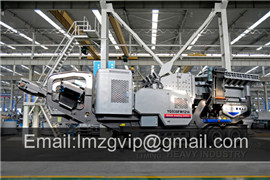
AMIT 135: Lesson 7 Ball Mills
Mill Type Overview. Three types of mill design are common. The Overflow Discharge mill is best suited for fine grinding to 75 106 microns.; The Diaphram or Grate Discharge mill Laboratory Ball Mills for Ultrafine ,This means that when the sun wheel rotates once, the grinding jars rotate twice in the opposite direction. Figure 4. In the planetary ball mill, centrifugal Optimization of Cement Grinding Operation in Ball Mills,The second chamber is the fine grinding chamber. It is lined with classifyingtype mill shell liners and provided with finer ball charge. Classifying liners ensure that the ball charge is segregated along the length of the chamber keeping larger grinding media at the beginning of the compartment and smaller media towards the end of the

MODELING THE SPECIFIC GRINDING ENERGY AND BALL
21 CONCLUSIONS Continued In the present work, equations were also derived, giving: zthe ballmill power drawP as a function of its dimensions: internal mill diameter D and length L, zthe ballmill power drawP as a function of the feed D f (mm) and the product size d (mm), the Bond work index w i (kWh/short ton) and the mill throughput Performance optimization of an ,The energy consumption in the ball mill was found to be 6.5 kWh/t of ore with a targeted product size below 1 mm. The BWI of the ores varied from 5.8 to 7.8 kWh/t to reduce the Tailoring fine particle size distributions by air swept ball ,Abstract. Fine grinding in an air swept and a grate discharge ball mill working in closed circuit with a forced vortex air classifier has been investigated in continuous laboratory scale. Minerals with different physical properties were ground down to 40, 20, and 10 micron top size. The shape of the product particle size distribution curve

Cement Grinding Cement Plant Optimization
Cement grinding operation may be performed in one of the following mill setups. Ball and tube mills. Vertical Roller Mills (VRM). Roller press with Ball mill. Ball Mill. Ball mills with high efficiency separators have been used for cement grinding in cement plants all these years. Ball mill is a cylinder rotating at about 7080% of criticalChecking your browser Pharmapproach,The balls which could be of different diameter occupy 30 50 % of the mill volume and its size depends on the feed and mill size. The large balls tend to break down the coarse feed materials and the smaller balls help to form fine product by reducing void spaces between the balls. Ball mills grind material by impact and attrition.Steatite Ceramic Grinding Balls and Media Steatite ,Steatite ceramic balls and mill lining bricks are manufactured from the same finegrained composite and are ideal performance partner. Thus, they retain their shape better and last longer than flint / river pebbles, natural stones, porcelain etc. Due to their higher density, hardness, toughness and a higher degree of sphericity, Steatite ceramic grinding media