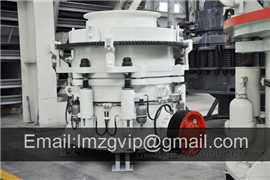
Grinding mills for mining and minerals processing
Fruitful Outotec has over 100 years of experience in horizontal grinding mills and has always been an industryleader in innovative technology. Fruitful Outotec's unmatched expertise ensures delivery of your Premier™ mill or Select™ mill based on your operational needs. Rod Mills Grinding Mills DOVE DOVE EQUIPMENT ,DOVE supplies 2 models of small Rod Mills designed for laboratories milling process, capacity range of (5000g/Hr 20 Kg/Hr). For small to large scale grinding Rod Mills for Mining Market to Reflect ,The latest report on the Rod Mills for Mining Market provides a comprehensive overview of the industry’s important characteristics, including Dianzhong Mining
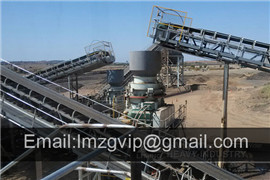
Grinding Mills Westpro Machinery
Grinding Mills. Westpro’s heavy duty grinding mills are designed for durability and excellent grinding performance in mining applications. 6ft Diameter x10ft Rod Mill,Rod Miller,Grinder MachinefdfdsfsdfHongji Group,Rod mill is widely used grinding machine to grind all kinds of ore and rocks in metal and nonmetal mining, water conservation, building materials, sand making Rod Mills Mineral Processing,Rod Mills may be considered either fine crushers or coarse grinding equipment. They are capable of taking as large as 2″ feed and making a product as fine as
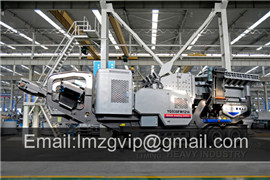
Rod Mill Grinding Rods
Unfortunately, plant studies on media size versus rod mill performance are rare. The single case that was found was once again from Tennessee Copper. A Fruitful peru mining machinery rod mill.md at main · ,Contribute to changjiangsx/Fruitful development by creating an account on GitHub.Comparative Analysis of Rod Mill and Ball Mill,The reason why rod mill is called rod mill is that its grinding medium is steel rod, while the grinding medium of ball grinding mill is steel ball. Because the shape of the

6 Of The Best CNC Mills (And LowCost Alternatives)
Tormach PCNC 440 Best CNC Mill for Schools and Universities. Price: From $5,390. Tormach is a wellknown name when it comes to CNC mills and the PCNC Rod Mills Price, 2023 Rod Mills Price Manufacturers,Rod Mills Price Select 2023 high quality Rod Mills Price products in best price from certified Chinese Cnc Mills manufacturers, Mineral Rod Mill suppliers, wholesalers and factory on MadeinChina 3050t/Hr 2100*3000 Good Quality Rod Mill Machine for Mining Industry, Ore Rod Mill Machine Recommended product from this supplier.Grinding Mills Westpro Machinery,Grinding Mills. Westpro’s heavy duty grinding mills are designed for durability and excellent grinding performance in mining applications. 6ft Diameter x10ft Ball and Rod Mills at the Westpro Shop ADVANTAGES. Sizes up to 4.9m (16tf) diameter and 4500hp (3356KW) Available with rubber, steel or ceramic liners; APPLICATIONS. Size
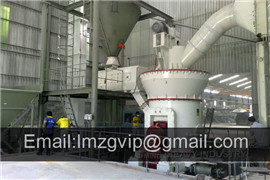
AMIT 135: Lesson 8 Rod Mills Mining Mill Operator
Typically R = 8. Rod Mill Charge: Typically 45% of internal volume; 35% 65% range. Bed porosity typically 40%. Height of bed measured in the same way as ball mills. Bulk density of rods = 6.25 tons/m3. In wet grinding, the solids concentration 1s typically 60% 75% by mass. A rod in situ and a cutaway of a rod mill interior.Zhengzhou Mega Industry Co., Ltd. mining ,mining machinery,ball mill,cement production line,jaw crusher,act Ball Mill & Rod Mill; China professional grinding mill; rod mill, grinding mill; Large capacity ball mill, Big ball mill, with the Best Quality China top quality ball mill; Product Showcase Jaw Crusher, Stone Crushing Jaw CrusherWear of grinding media in the mineral processing,Within the mineral processing industry, a range of grinding conditions exists which include semiautogenous grinding (SAG), rod milling, and conventional ball milling. Each of these mill environments presents a unique environment for grinding media, requiring the application of specific physical and chemical properties for optimum grinding media performance. The

7 Differences Between Ball Mill and
Although they have the similar working principle, there are many differences between ball mill and rod mill on details. 1. Configuration of ball mill and rod Rotary drum mill, Rotary drum grinding mill DirectIndustry,mill with rods SMP series. horizontal for plastics for pipes and profiles. Output: 100 kg/h 1,400 kg/h. Motor power: 6, 75 kW. Machine weight: 900 kg 4,200 kg. The SMP series for the processing of profiles and pipes. These are selffeeding machines with a horizontal feed hopper for bars measuring six metres or more in length.Fruitful peru mining machinery rod mill.md at main · ,Contribute to changjiangsx/Fruitful development by creating an account on GitHub.
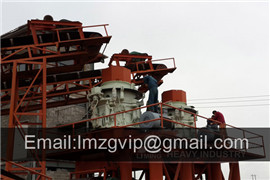
TECHNICAL NOTES 8 GRINDING R. P. King Mineral Tech
Figure 8.2 Media motion in the tumbling mill. 8.1 Grinding 8.1.1 Grinding action Industrial grinding machines used in the mineral processing industries are mostly of the tumbling mill type. These mills exist in a variety of types rod, ball, pebble autogenous and semiautogenous. The grinding action is induced by relative motion between theHow it Works: Crushers, Grinding Mills ,The feed enters one end of the ball mill, and discharges out the other end. Ball mills vary greatly in size, from large industrial ball mills measuring more than 25 ft. Rod Mills for Mining Market to Reflect ,The latest report on the Rod Mills for Mining Market provides a comprehensive overview of the industry’s important characteristics, including Dianzhong Mining
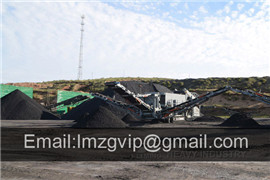
Highly Efficient Rod Mill Fote
Rod mill on working site. 1 The rod mill usually uses a steel rod with a diameter of 50100 mm as a grinding medium. The length of the steel rod is 2550 mm rod mill manufacturers ,grinding rod supplier walker,JXSC Machine uses advance technology to manufacture the rod mill. So our rod mills are greatest efficiency, easy to operate, effective and energy saving. They are popular in the mining industry. The rod mill is composed by the feeding part, feeder part, discharging part, cylinder part, main bearing part and driving part.AMIT 135: Lesson 8 Rod Mills Mining Mill Operator ,Typically R = 8. Rod Mill Charge: Typically 45% of internal volume; 35% 65% range. Bed porosity typically 40%. Height of bed measured in the same way as ball mills. Bulk density of rods = 6.25 tons/m3. In wet grinding, the solids concentration 1s typically 60% 75% by mass. A rod in situ and a cutaway of a rod mill interior.
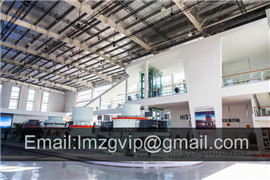
7 Differences Between Ball Mill and
Although they have the similar working principle, there are many differences between ball mill and rod mill on details. 1. Configuration of ball mill and rod Ball Mills Industry Grinder for Mineral Processing JXSC ,Ball Mills Capacity】 0.290 T/H Advantages】Designed for long service life, minimum maintenance, can grind and homogenize mineral ores down to the nano range, a large volume of processing capacity Max Feeding Size】 <25mm Discharge Size】0.0750.4mm Types】Overflow ball mills, grate discharge ball mills Service】 24hrs TECHNICAL NOTES 8 GRINDING R. P. King Mineral Tech,Figure 8.2 Media motion in the tumbling mill. 8.1 Grinding 8.1.1 Grinding action Industrial grinding machines used in the mineral processing industries are mostly of the tumbling mill type. These mills exist in a variety of types rod, ball, pebble autogenous and semiautogenous. The grinding action is induced by relative motion between the

Factors Influence Ore Grinding Mill Efficiency JXSC Mining
Abstract. The grinding efficiency is the most important parameter to evaluate machine performance. This article discussed the factors that influence grinding efficiency including article size to mill machine,milling medium,slurry rheological properties,underflow ratio,liner,grinding aid etc. The mill machine should be The Working Principle and Structure of Rod Mill Mining ,Rod mill main bearing structure adopted, for example, the totally enclosed type "joystick," since a selfaligning bearing, bearing bush runs round the high pressure oil cavity, central axis of babbitt alloy layer with a "snake" in the cooling water pipe, oil used with a combined type ZDG 63 a high and low pressure pump station, by oil tubeInching drives one way to improve mill safety Fruitful ,The typical mechanical inching drive motor speed is around 1500 to 1800 RPM while the mill inching speed is in the order of 0.1 to 0.15 RPM. Thus, the gear reduction ratio between the inching drive motor and the mill is roughly 12,000 to 1. What this means is that the inching drive motor must turn 12,000 times to be able to turn the mill once.