
ThyssenKrupp Industrial Solutions Leading engineering
The convex geometry of the grinding roller, that proved superior in the classical doublerollerpair mill with regard to wear, has been retained. This geometry Conditioning and monitoring of grinding wheels CIRP,and regeneration of the grinding wheel macro and micro geometry influencing the grinding wheel topography. According to Spur, conditioning is classified Calculation of grinding wheel ,The mathematical description of the target geometry that is needed for the calculation of the maximum grinding wheel diameter bases on a 2D calculation ( fig. 3). Here, the
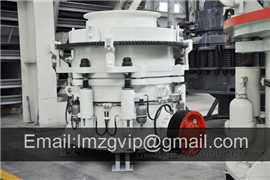
Powder fineness to d = 10 µm PRINCIPLE OF
hand to the design of the grinding chamber, especially the table and roller geometry. Hosokawa Alpine retained the wellknown advantages and refined the grinding Grinding Wheel an overview ScienceDirect Topics,Grinding and finishing processes. Mark J. Jackson, in Modern Machining Technology, 2011 4.2.6 Modifications to the grinding process. When the grinding wheel and dressing wheel How Tapered Roller Geometry ,rev/sec per roller geometry tested, five rollers were sampled after 20, 40, and 60 min. grind interva ls. OOR for OOR for the 15 rollers was measured at the LED,
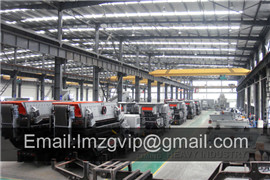
Machining 101: What is Grinding? Modern Machine Shop
Evan Doran. Associate Editor. On its surface, grinding seems simple: a machine takes a rotating tool (usually a wheel) with abrasive grains and applies it to a Effects of the grinding conditions on geometry of ,For the grinding of microstructured functional surfaces called riblets, a novel dressing strategy using diamond profile rollers was introduced for the generation of How Tapered Roller Geometry Determines Bearing ,roller geometry effects on OOR differed over 60 minute grind intervals. Craig Seidelson / International Journal of Engineering Science and Technology (IJEST) ISSN: 09755462
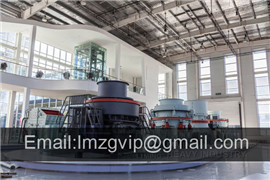
Grinding Machine [Grinding Wheel,
Small wheels of 25mm diameter cost up to 10$ for conventional abrasive and for diamond up to 200$.; Large wheel of 500mm diameter and 250mm width, the ThyssenKrupp Industrial Solutions Leading engineering ,The convex geometry of the grinding roller, that proved superior in the classical doublerollerpair mill with regard to wear, has been retained. This geometry makes long service lives possible and provides a constant performance profile for both throughput and energy requirement throughout the entire lifetime of the grinding elements. ThePowder fineness to d = 10 µm PRINCIPLE OF ,hand to the design of the grinding chamber, especially the table and roller geometry. Hosokawa Alpine retained the wellknown advantages and refined the grinding technology to develop table roller mills for ultrafine end products down to d 97 = 10 µm. A complete size range of these optimized mills was developed to address present as

Book The Mechanics of Rollers TAPPI
5 Roller Geometry Axial 5 Roller Geometry Diametral 6 Shell Materials 6 Coverings and Coatings 7 To Drive or Not to Drive 7 Roller Drives 8 Roller Issues Grinder 254 Inplane Misalignment 155158, 160 Justification 9 Landmarks 165 Level 161, 165, 248 Methods 9, 155, 248TECHNICAL SOLUTIONS FOR GRINDING Norton ,a function of roller geometry. CYLINDRICAL ROLLER STATIONS STONES ROLLERS ROLLER THRUFEED Throughfeed superfi nishing Centerless throughfeed Double disc grinding DIAMETER RECTIFICATION Abrasive wheels and stones for ball & roller grinding, finishing, and lapping. 18 ROLLING ELEMENTS BALL GRINDING, FINISHING Grinding Machines SpringerLink,As grinding machines belong to the class of machines for the material removal with geometrically nondefined cutting edges, those machines can be classified in correlation to the classification of the different process technologies with geometrically nondefined cutting edges as it is given in DIN 8589, parts 11, 12, and 13 (DIN 858911 2003;
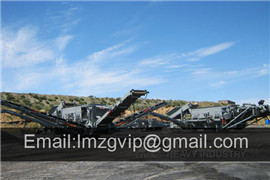
Grinding Force an overview ScienceDirect Topics
Grinding Force Ratio. Grinding force ratio is a parameter that gives indirect information about the efficiency of grinding. Force ratio is defined as: (2.8) When grinding with sharp wheels grinding force ratio is high since normal force is low compared to tangential force. Conversely, when grinding with blunt wheels grinding force ratio is low.Fundamentals of Roll Cooling and Control of Flatness at ,Footprint Geometry Effective and precise Footprint Geometry is the fundamental requirement to establish a Homogeneous Cooling application and is achieved by the configuration of a uniform Cooling Area on the work roll, formed by the impingement of an array of adjacent sprays, equally spaced and positioned to assure consistent SIZE REDUCTION akahl,Number of rollers 3 5 3 4 3 6 Roller speed m / s 2,5 2,5 2,5 Drive motor kW / min1 160 200 / 1500 200 250 / 1500 200 315 / 1500 Type 55 1500 65 1250 60 1500 Die diameter mm 1500 1250 1500 Roller diameter / width mm 450 / up to 240 450 / up to 190 450 / up to 240 Number of rollers 4 6 4 5 4 6

Cylinder Smarts Guide to Essential Gravure Technology
Runout, or TIR is a measurement of the relative accuracy between all the diametrical planes of the base.. Size of the base is determined to accommodate the amount of copper that the Engraver requires for their process, typically between 0.012” and 0.020” in diameter.. Finish of the base body needs to be suitable for the copper plating process.. Vibration Analysis Schaeffler Group,Vibration Analysis Schaeffler GroupRolling bearings in the world’s largest vertical roller mill,Grinding roller diameter 2500 mm Grinding roller speeds up to 45 min–1 Loads on individual grinding roller bearings: Radial forces up to 2800 kN Axial forces up to 300 kN Basic rating life min. 80000 h Lubrication and sealing Grinding dust, process heat and heavy flow conditions in the equipment place extreme requirements

TECHNICAL SOLUTIONS FOR GRINDING Norton
a function of roller geometry. CYLINDRICAL ROLLER STATIONS STONES ROLLERS ROLLER THRUFEED Throughfeed superfi nishing Centerless throughfeed Double disc grinding DIAMETER RECTIFICATION Abrasive wheels and stones for ball & roller grinding, finishing, and lapping. 18 ROLLING ELEMENTS BALL GRINDING, FINISHING Fundamentals of Roll Cooling and Control of Flatness at ,Footprint Geometry Effective and precise Footprint Geometry is the fundamental requirement to establish a Homogeneous Cooling application and is achieved by the configuration of a uniform Cooling Area on the work roll, formed by the impingement of an array of adjacent sprays, equally spaced and positioned to assure consistent Study on threedimensional topography modeling of the ,As shown in Fig. 14, the single crystal corundum grinding wheel is trimmed by the diamond roller on the slider grinding machine and the specific experimental parameters are given in Table 2. To ensure the rationality and accuracy of the wheel topography measured, six different locations areas with
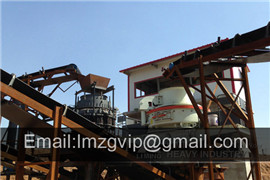
Effects of the grinding conditions on geometry of
Precision grinding is a promising method for machining microstructured surfaces. Controlling microstructured surface geometries provides interesting insights into the optimisation of their usage based on the application fields. This requires an understanding of the effects of the factors influencing the grinding process. The effects of Vibration Analysis Schaeffler Group,Vibration Analysis Schaeffler GroupThe Global High Pressure Grinding Roller (HPGR) Market size,The Global High Pressure Grinding Roller (HPGR) Market size is expected to reach $549.1 million by 2028, rising at a market growth of 5.8% CAGR during the forecast period

The Fundamentals of Thread Rolling CJWinter
The Benefits of Thread Rolling. The fastest, most economical method for producing highly accurate threads, thread rolling allows for higher repeatability, stronger threads, and better finish quality and mechanical properties than grinding, cutting, or chasing. Rolling stock has a smaller diameter than fullsized cutting stock, so no material High Pressure Grinding Roller Presses KHD (高压磨辊压,High Pressure Grinding Roller Presses KHD (高压磨辊压 KHD).pdf,2 6 6 4 1 4 3 7 5 5 12 8 10 13 9 11 RPS Design Features • Removal of both rolls to one side, • Permanently mounted frame •Gearbox assembly/dismounting without frameThree factors affecting the surface ,In the grinding with superabrasive grinding wheels, a truing tool or roller dresser is used for truing. Vitrified bond dressing rods are used for sharpening.