
Semiconductor Thickness Measurement & Wafer
With MEMS, wafer thinning also controls the proof mass for devices such as accelerometers or the diaphragm thickness for pressure sensors. Etching the surface of the wafer produces the IC but grinding the backside is what produces the wafer’s desired thickness. During The backend process: Step 3 Wafer backgrinding,The Backgrinding Process. To improve the productivity of an operation, a multistep grinding operation is generally performed. The first step uses a large grit to coarsely grind the Effects of wheel spindle vibration on surface formation in ,Furthermore, the formation principle of grinding marks has been studied in depth during wafer selfrotational grinding. Pei et al. proposed a theoretical model to
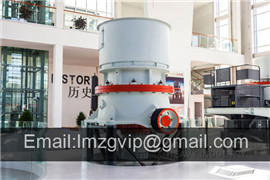
Fine grinding of silicon wafers: designed experiments
The grinding force measured is the interaction force between the grinding wheel and the wafer in the direction parallel to the spindle axis. It is also the direction Warping of Silicon Wafers Subjected to Backgrinding ,Gao et al. 92 investigated warping of silicon wafers in ultraprecision grindingbased backthinning process and then established a mathematical model to Working principle of wafer grinderAM Technology Co., Ltd.,Working principle of wafer grinder . Time:0819 13:57:48 Views:10. Wafer grinder is a kind of semiconductor equipment, which is mainly used for
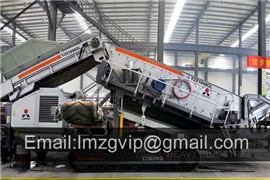
Warping of silicon wafers subjected to backgrinding
Warp model in wafer backthinning 2.1. Force analysis The grindingbased backthinning process is featured with a rotating wafer which is held by a vacuum chuck [3,8]. The principle of grinding wafer,1015 Since BGWOR is also based on the principle of selfrotating grinding, the formula of grinding marks on the surface of the wafer is almost the alike as that in chuck BASIC PRINCIPLE OF GRINDING UNDERSTANDING ,Grinding is the most common type of material cutting and surface generation process. Mostly grinding process is used to shape and to provide better finishing parts of

principle of grinding wafer
In MEMS wafer processing, the capping of fragile mechanical structures using wafer bonding is a very Mar 15, · 3 Grinding Uniple A Circumference 背面研磨(Back Grinding)决定晶圆的厚度 SK hynix Newsroom,经过前端工艺处理并通过晶圆测试的晶圆将从背面研磨(Back Grinding)开始后端处理。. 背面研磨是将晶圆背面磨薄的工序,其目的不仅是为了减少晶圆厚度,还在于联结前端和后端工艺以解决前后两个工艺之间出现的问题。. 半导体芯片(Chip)越薄,就能堆叠Warping of silicon wafers subjected to backgrinding process,Wafer thinning experiments were performed on a wafer grinder (VG401 MK II, Okamoto, Japan), as shown in Fig. 10. Cuptype grinding was adopted in accordance with the principle of wafer rotation grinding. An online thickness measurement device was incorporated into the grinding system to monitor wafer thickness.

The backend process: Step 3 Wafer backgrinding
The Backgrinding Process. To improve the productivity of an operation, a multistep grinding operation is generally performed. The first step uses a large grit to coarsely grind the wafer and remove the bulk of the excess wafer thickness. A finer grit is used in the second step to polish the wafer and to accurately grind the wafer to theFine grinding of silicon wafers: designed experiments,The grinding force measured is the interaction force between the grinding wheel and the wafer in the direction parallel to the spindle axis. It is also the direction perpendicular to the wafer surface. The maximum force during the entire grinding cycle is used for analysis. The monitor of the grinder displays the spindle motor currentJ.H. Liu,Z.J. Pei,Graham R. Fisher CORE,process is referred to conventional wafer grinding in this paper. During grinding, the diamond grinding wheel and the wafer rotate about their own rotation axes simultaneously, and the wheel is fed towards the wafer along its axis. The rotation axis for the grinding wheel is offset by a distance of the wheel radius relative to the rotation axis

Effects of wheel spindle vibration on surface formation in
Furthermore, the formation principle of grinding marks has been studied in depth during wafer selfrotational grinding. Pei et al. proposed a theoretical model to analyze the grain trajectory [60], simulated wafer shapes under different wheel setup parameters [61] and further discussed the influence of chuck geometry on the grinding Simultaneous double side grinding of silicon wafers: a ,wheel is a diamond cup wheel. The grinding wheel and the wafer rotate about their own rotation axes simultaneously, and the wheel is fed towards the wafer along its axis [9,12,13]. After the wafer front side is ground, the grinder flips the wafer over and continues to grind the back side. The advantages of SSG over lapping include [10,12–14]:Process Research to Improve the Edge Processing ,In this paper, the 200 mm silicon wafers are analyzed and studied from the principle of silicon wafer edge grinding, the chuck speed, the chamfering wheel speed and the edge polishing efficiency. Then, the influence of different processing conditions on the

The process of backside grinding of silicon wafer
Now the diameter of more than 200mm of large size silicon wafer backgrinding (backgrinding) mostly adopts the ultraprecision grinding technology based on the principle of white rotary silicon wafer grinding. Silicon wafer back grinding is generally divided into two steps: rough grinding and fine grinding. In the rough grinding stage, theMETHOD OF GRINDING WAFER AND GRINDING WHEEL,The grinding wheel is positioned at a rotation center P1 of the wafer 11 so that the first grinding wheel 80 passes, the chuck table 54 is rotated while the cutting wheel is rotated, and the wafer is ground by the first andsecond grinding wheels 80, 82.;COPYRIGHTStudy into grinding force in back grinding of wafer with ,Back grinding of wafer with outer rim (BGWOR) is a new method for carrierless thinning of silicon wafers, and its working principle is shown in Fig. 1. Different from conventional back grinding, the BGWOR process only grinds the inner area of the silicon wafer and leaves a rim (approximately 3–5 mm) on its outer circumference [ 4, 5, 6 ].

Fine grinding of silicon wafers: designed experiments
The grinding force measured is the interaction force between the grinding wheel and the wafer in the direction parallel to the spindle axis. It is also the direction perpendicular to the wafer surface. The maximum force during the entire grinding cycle is used for analysis. The monitor of the grinder displays the spindle motor currentWafer Thinning: Investigating an essential part of ,Wafer thinning is a part of the semiconductor manufacturing process. It is essentially grinding off the backside of the wafers to control their thickness and is useful for the production of ultrathin wafers. These flattened wafers are used to effect stacked and highdensity packaging in compact or microelectronic devices. This article discusses the The backend process: Step 3 Wafer backgrinding,The Backgrinding Process. To improve the productivity of an operation, a multistep grinding operation is generally performed. The first step uses a large grit to coarsely grind the wafer and remove the bulk of the excess wafer thickness. A finer grit is used in the second step to polish the wafer and to accurately grind the wafer to the

Research on the shape of ground wafer in Back Grinding
DOI: 10.1016/j.mssp..106344 Corpus ID: 244655999; Research on the shape of ground wafer in Back Grinding of Wafer with Outer Rim @article{GuoResearchOT, title={Research on the shape of ground wafer in Back Grinding of Wafer with Outer Rim}, author={Xiaoguang Guo and Wei Hao Yao and Semiconductor BackGrinding IDCOnline,Semiconductor BackGrinding The silicon wafer on which the active elements are created is a thin circular disc, typically 150mm or 200mm in diameter. During diffusion and similar processes, the wafer may become bowed, but wafers for assembly are normally stress relieved and can be regarded as flat.The process of backside grinding of silicon wafer,Now the diameter of more than 200mm of large size silicon wafer backgrinding (backgrinding) mostly adopts the ultraprecision grinding technology based on the principle of white rotary silicon wafer grinding. Silicon wafer back grinding is generally divided into two steps: rough grinding and fine grinding. In the rough grinding stage, the

Formation of subsurface cracks in silicon wafers by grinding
Generally, SSCs are induced in a silicon wafer during the machining process. Danilewsky et al. and Rack et al. studied crack propagation and fracture mechanisms in silicon wafers under thermal stress conditions using an insitu Xray diffraction imaging technique. 26,27 26. Rack A, Scheel M, Danilewsky AN. Realtime Warping of silicon wafers subjected to backgrinding ,Warp model in wafer backthinning 2.1. Force analysis The grindingbased backthinning process is featured with a rotating wafer which is held by a vacuum chuck [3,8]. The wafer is induced with stresses by grinding which are partially released when the wafer is removed from the chuck. Residual stresses are thus left in the ground wafer. InMETHOD OF GRINDING WAFER AND GRINDING WHEEL,The grinding wheel is positioned at a rotation center P1 of the wafer 11 so that the first grinding wheel 80 passes, the chuck table 54 is rotated while the cutting wheel is rotated, and the wafer is ground by the first andsecond grinding wheels 80, 82.;COPYRIGHT