
Electrical Discharge Machining (EDM) and Grinding (EDG)
Electrical discharge machining. Removes any electrically conducting material by high frequency sparks that arc through a dielectric fluid flowing between the negatively charged workpiece and the positively charged, tubular or solid tool. The tool is servo Electrochemical Discharge Grinding ASM Digital Library,Electrochemical discharge grinding (ECDG) is a combination of electrochemical grinding (ECG) and electrical discharge grinding (EDG), with some modification of each. This Electrical Discharge Grinding Machining ASM Digital ,Electrical discharge grinding (EDG) is much like electrical discharge machining except that the electrode (tool) is a rotating graphite wheel. This article commences with a schematic
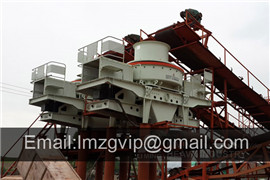
Electrical Discharge Diamond Grinding (EDDG): A Review
So, a new hybrid machining process (HMP) has been discovered, namely electrical discharge diamond grinding (EDDG). This EDDG is the combination of electric Optimization of the Interelectrode Gap in Electrical ,The processing zone for electrodischarge diamond grinding is where the cutting grains of the wheelwork in the interelectrode gap, where the discharges act. Experimental investigations on electrical discharge ,Experimental study and parameter design of electro discharge diamond grinding. Int. J. Adv. Manuf. Technol., 36 (2008), pp. 3442. Google Scholar. J. Xie, J.
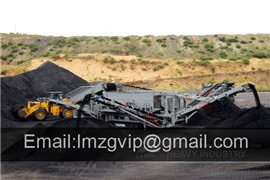
Wire ElectroDischarge Grinding for MicroMachining
A new method, WEDG (wire electrodischarge grinding), for EDM'ing very thin rods is proposed. Travelling wire is used as the tool electrode. However, the wire Electro discharge grinding process. Download Scientific ,Balbir Singh. Electrical Discharge Machining (EDM) is a controlled metalremoval process that is used to remove metal by means of electric spark erosion. In this process an Difference Between EDM and EDG ,Electro Discharge Machining (EDM) Electro Discharge Grinding (EDG) A form electrode made of electrically conductive metal is used as cathode. So spark
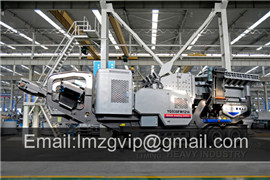
Electrical discharge grinding Find
The process. The tool consists of a disc [1], which rotates around its horizontal axis. Connection via power supply makes the disc act as the cathode and EDG Electric Discharge Grinding novick.eu,Electro chemical discharge grinding. Electrochemical discharge grinding (ECDG) is a hybrid process of electrochemical machining (ECM) and electrical discharge grinding (EDG). It is used for the machining of electrically conductive materials. This process uses nonabrasive graphite grinding wheel with no abrasive particles and an electrolyte.Optimization of the Interelectrode Gap in Electrical ,The processing zone for electrodischarge diamond grinding is where the cutting grains of the wheelwork in the interelectrode gap, where the discharges act. Electric discharges in the grinding zone act on the cutoff chips, on the surface of the workpiece material, and on the grinding wheel on the bond in the intergranular space and
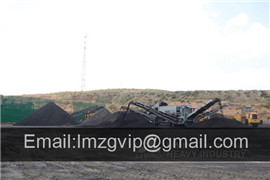
Electro discharge grinding process. Download Scientific
Balbir Singh. Electrical Discharge Machining (EDM) is a controlled metalremoval process that is used to remove metal by means of electric spark erosion. In this process an electric spark is usedElectrical Discharge Diamond Grinding (EDDG): A Review,So, a new hybrid machining process (HMP) has been discovered, namely electrical discharge diamond grinding (EDDG). This EDDG is the combination of electric discharge machining (EDM) and grinding wheel with metalbonded diamond grit. EDDG gives better performance than EDM due to the spark generation the rotating diamond Electrical Discharge Grinding of Polycrystalline ,Electrical discharge grinding (EDG) is becoming more prevalent in the manufacturing of polycrystalline diamond (PCD) tools. This paper concerns investigation of the effects of machining parameters, as well as finishing infeed, to the surface quality obtained when using EDG to erode PCD. With the aid of the morphological findings,
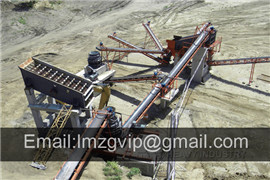
Fabrication of microelectrode with large aspect ratio and
The wire electrodischarge grinding (WEDG) is one of the most widely used methods to fabricate microelectrode, and it offers the benefit of sustaining good grinding accuracy by feeding fresh wire during the whole fabricating process (Masuzawa et al., 1985). Based on this method, some evolutions have been made in different ways.Electrical discharge grinding Find ,The process. The tool consists of a disc [1], which rotates around its horizontal axis. Connection via power supply makes the disc act as the cathode and Electrochemical Grinding: Working, Application, ,In Electrochemical grinding, the metal bonded grinding wheel filled with a nonconductive abrasive. The grinding wheel act as a cathode and the workpiece is act as an anode. The electrolyte, which is usually sodium nitrate, sodium chloride, potassium nitrite, with a concentration of 0.150 to 0.300 kg/litre of water.

Diamond Face Grinding of WCCo Composite with Spark
electro discharge diamond grinding (EDDG) process is developed. The effect of input parameters such as wheel speed, current, pulse ontime and duty factor on output parameters such as material removal rate (MRR), wheel wear rate (WWR) and average surface roughness (ASR), are investigated. The present study shows that MRRModeling of silicon ingot slicing process by wire–electrical ,Modeling of wire–electrical discharge machining is difficult as it involves several disciplines such as thermodynamics, hydrodynamics, electrodynamics and electromagnetics. Various researchers have proposed analytical models for electrical discharge machining and wire–electrical discharge machining through the use of Electrical Discharge Grinding Machining ASM Digital ,Electrical discharge grinding (EDG) is much like electrical discharge machining except that the electrode (tool) is a rotating graphite wheel. This article commences with a schematic illustration of a setup for EDG wheels and discusses the control operation of the EDG setup. It tabulates typical applications and conditions for the EDG of

Electrical discharge grinding Find
The process. The tool consists of a disc [1], which rotates around its horizontal axis. Connection via power supply makes the disc act as the cathode and Developments in Electrical Discharge Grinding process: A ,These are: electro discharge cutoff grinding, electrodischarge face grinding and electrodischarge surface grinding. In cutoff grinding configuration, the metallic wheel Fig. 5 Input parameters and process outputs for EDG rotates about its horizontal axis and fed into process perpendicular direction to the machine table.MICRO ELECTRODISCHARGE MACHINING: ,Wire ElectroDischarge Grinding (WEDG) 4 1.3. Poly Crystalline Diamond (PCD) Grinding 6. 1.3.1. Poly Crystalline Diamond Tools 6 1.3.2. Ductile Mode Grinding of Brittle Materials 7 . 1.4. Thesis Overview 10. 1.4.1. Thesis Hypothesis 10 1.4.2. Thesis Contents Overview 10 . Chapter 2. Precision of Micro Shafts Machined with WEDG 11
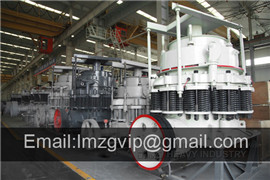
Diamond Face Grinding of WCCo Composite with Spark
electro discharge diamond grinding (EDDG) process is developed. The effect of input parameters such as wheel speed, current, pulse ontime and duty factor on output parameters such as material removal rate (MRR), wheel wear rate (WWR) and average surface roughness (ASR), are investigated. The present study shows that MRRelectro discharge grinding machine ppt.md at main · ,Contribute to dinglei/en development by creating an account on GitHub.Electrochemical discharge machining: Principle and ,temperature of the discharge itself has been estimated by emission spectroscopy (Reghuram 1994) for different electrolytes with varying concentration. The temperature is found to be in the range 800(O10 000 K. Thus, it is possible to cause material removal in very small quantities by melting and evacuation if the workpiece is kept very
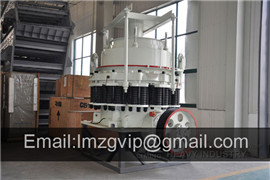
Modeling of silicon ingot slicing process by wire–electrical
Modeling of wire–electrical discharge machining is difficult as it involves several disciplines such as thermodynamics, hydrodynamics, electrodynamics and electromagnetics. Various researchers have proposed analytical models for electrical discharge machining and wire–electrical discharge machining through the use of Electric Discharge Machining (EDM) ,3. Electric discharge machining (EDM), sometimes colloquially also referred to as spark machining, spark eroding, burning, die sinking or wire erosion, is a Electrochemical Machining: Definition, ,Applications of Electrochemical Machining . As mentioned earlier in the article ECM is used for heavy machining of hard materials which cannot be machined using conventional