
Cement Production an overview ScienceDirect Topics
Typical raw materials used for cement production have 85% cayenne, 13% clay or blackboard, and under 1% each of materials such as silica, alumina, and iron ore. These feedstocks are crushed into particles with a diameter of less than 20 World cement CEMENT RAW MATERIALS International Cement Review,2.1 Extraction The raw materials used in cement manufacture are extracted in large quarries, typically with outputs of up to, or over, 2.5 million tonnes per year. Raw materials for cement manufacturing Cement Plant ,Lime Component Limestone: Common forms of calcium carbonate used as raw material for cement manufacturing are limestone and chalk.Limestone is of predominantly fine

RAW MATERIALS IN CEMENT
The main materials used in cement production are minerals containing calcium oxide, silex, Calculating the cost of 1 ton of ,A plan to increase the coprocessed iron/steel slag at cement facilities (from 1 to 10 per cent) would translate into substantial gains in material raw material need for 1 ton cement production,how many tonnes of limestone needed for cement Machine, It takes approximately 3,400 lbs. of raw materials to make one ton (2,000 lbs.) limestone needed for 1 ton cement
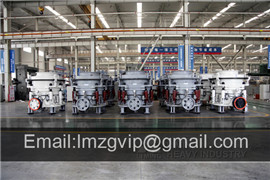
limestone needed for 1 ton cement production
Product You Need: *, limestone is the main raw material for Cementmaking Production. It needs about 1.3 tons Go to Product Center. iron ore required to produce 1 ton of ~liagceng/Fruitful: raw material need for 1 ton cement ,Fruitful/raw material need for 1 ton cement production.md rwrr 20.5 KiB . View; Log; Blame; View raw; 29dbe9ef — liach first 2 months agoRaw Material Need For 1 Ton Cement Production Htm ,The Greenhouse Gas Emission From Portland Cement. Jun 24 we assume that various raw materials of cement are transported by trucks 5 ton deadweight and the
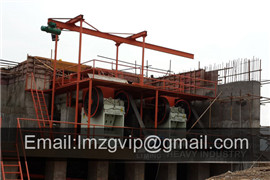
raw material need for 1 ton cement production
raw material need for 1 ton cement production . price of ballast grinding machine in kenya . Vertical Tamper RobelRotation ensures that the (PDF) Analysis of material flow and ,The results show that approximately 2.48t, 4.69t, and 3.41t of materials are required to produce a ton of the product in raw material preparation, clinker CEMENT RAW MATERIALS International Cement Review,2.1 Extraction The raw materials used in cement manufacture are extracted in large quarries, typically with outputs of up to, or over, 2.5 million tonnes per year. Typically about 1.65 tonnes of limestone (1.5 to 1.8 tonnes) and 0.4 tonnes of clay are quarried for each tonne of cement produced.
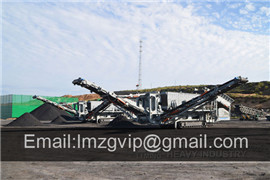
RAW MATERIALS IN CEMENT
The main materials used in cement production are minerals containing calcium oxide, silex, alumina and iron oxide. These components are rarely Cement Production Process Cement Manufacturing ,There are three steps of the hightemperature system: Drying or preheating, calcining, and sintering. The calcining is the core part of the clinker production; the raw meal is weighed and sent into preheater and cement kiln to process clinker. Grate cooler helps to cooler clinker, the cooled clinker is sent to the cement silo for storage.limestone needed for 1 ton cement production,Product You Need: *, limestone is the main raw material for Cementmaking Production. It needs about 1.3 tons Go to Product Center. iron ore required to produce 1 ton of clinker for cement, raw material need for 1 ton cement production raw material need for 1 ton cement as about 1.5 tons of limestone are needed to produce one ton of

Weighbelt Feeders in Cement
The global cement market produced 5.17 billion tons of cement in and the market is expected to grow by 3.3% each year from to 2026. This means How Much Does It Cost To Start A Cement Plant?,Today we’ll discuss the first part cement factory cost ( or cement plant cost). According to the data we know, the total cost of a cement plant is estimated to be US$ 17,000 to US$ 20,000 per ton. One thing to be clear, this is just an estimation, in the real cement plant building, the cement factory cost is affected by various factorsEnergy and Cost Analysis of Cement Production Using ,cement production is as low as $6 per tonne in China as opposed to $30 per tonne in Nigeria; this has contributed largely to the high and persistent rise in unit cost of ce ment production. There is thus the need for the adoption of energy efficiency in cement production in Nigeria. Recently, there has been an increasing interest in using
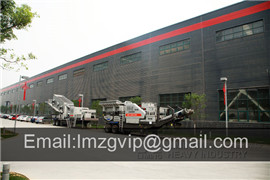
Indian Cement Industry: A Key Player in the Circular
18.3.1 Circular Supply Chain. In this head of circular economy, Indian cement industry is playing a key role by enhancing the application of Renewable Energy for electrical power generation. The renewable energy installed capacity (wind and solar) in cement plants increased by more than 40% to 276 MW from 2010 to .RAW MATERIAL OPTIMIZATION WITH NEURAL NETWORK ,The development of construction is presently experiencing rapid growth in Indonesia, leading to the requirement of the right materials for infrastructural enhancements. From the existing infrastructure, concrete innovations such as precasts are needed with good quality materials, for the quick completion of construction. This is because the need Cement Fuels & Technologies IEA,Cement emissions continue to rise, more investment in new technologies is needed. The direct CO2 intensity of cement production increased about 1.5% per year during . In contrast, 3% annual declines to 2030 are necessary to get on track with the Net Zero Emissions by 2050 Scenario. Sharper focus is needed in two key
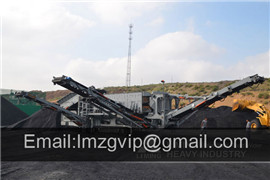
RAW MATERIALS IN CEMENT
The main materials used in cement production are minerals containing calcium oxide, silex, alumina and iron oxide. These components are rarely 6 Points in the Production Process to Optimize Cement ,Here are six categories of cement production that have potential for optimization. Raw Materials. The first step in the cement process is the recovery of the limestone and sometimes the extraction of clay. Online elemental analyzers can monitor material chemistry in real time, allowing for adjustments that will help extend the life of Steps of Cement Production Process Flyer Cement Silo,Preparation of raw materials. In the cement production process, each ton of portland cement requires the grinding of at least 3 tons of materials which include all kinds of raw materials (fuel, clinker, gypsum, mixture, etc.). Only a small percent of cement is packed in the bags only for those customers whose need is very small. The

Weighbelt Feeders in Cement
The global cement market produced 5.17 billion tons of cement in and the market is expected to grow by 3.3% each year from to 2026. This means How Much Does It Cost To Start A Cement Plant?,Today we’ll discuss the first part cement factory cost ( or cement plant cost). According to the data we know, the total cost of a cement plant is estimated to be US$ 17,000 to US$ 20,000 per ton. One thing to be clear, this is just an estimation, in the real cement plant building, the cement factory cost is affected by various factorsICESE045 Institute of Physics,materials on earth [1, 2]. The buildings sector is classified as the third largest CO 2 emitting institution worldwide [3, 4], with cement production figures stand at between 3.0 3.6Gt/year, and it has been estimated that per 1kg of cement produced, 0.50.9kg of CO 2 emissions are evolved, and this equates to about 3.24 billion tons of CO 2

Recent Progress in Newer Cementitious Binders as an
In the study, CSAB cement was developed by giving secondary heat treatment to primary raw materials such as—limestone, bauxite, phosphogypsum, at 1100–1200 °C for 1 h. ElAlfi and Gado [ 10 ] used kaolin (25%), gypsum (20%), marble sludge waste (55%) to develop CSAB cement at temperature of 1200 °C for 1 h.RAW MATERIAL OPTIMIZATION WITH NEURAL NETWORK ,The development of construction is presently experiencing rapid growth in Indonesia, leading to the requirement of the right materials for infrastructural enhancements. From the existing infrastructure, concrete innovations such as precasts are needed with good quality materials, for the quick completion of construction. This is because the need How much energy does it take (on average) to produce 1 ,The estimate for energy needed to produce 1kg of Aluminium is way off. According to Science Direct (which shows extract from per reviewed papers) the energy need to produce 1kg is more like 1315kWh (and not 60kWh as you quote) This is from information from Alcoa which is the largest producer of Aluminum