
Cement Raw Meal & Homogenization Process in The
The raw meal preparation process of the cement industry includes four links: mining, prehomogenization, grinding, and homogenization, which form the homogenization chain of Prediction of raw meal fineness in the grinding process of ,The accurate prediction of raw meal fineness in the vertical mill system is very helpful for the operator to control the vertical mill. However, due to the complexity of Analysis of material flow and consumption in cement ,In the surveyed cement plant, three balances are established between input and output material in the raw mill, clinker production, and cement grinding system.
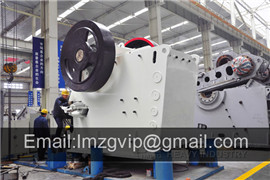
What Is Cement Milling? Difference Between Raw Mill And
Raw Mill and Cement Mill are essentially two different processes in a cement plant. Raw Mill is mainly used to grind raw materials into fine powder, whereas Raw Mill Raw Mill In Cement Plant AGICO Cement Raw ,Raw meal grinding is a vital link in the cement raw material preparation process. After the cement raw material is crushed, it will be sent into the raw mill for further grinding until a Raw Material DryingGrinding Cement Plant Optimization,Raw Material DryingGrinding. Drying of moisture in raw materials is required for effective grinding and subsequent handling of raw meal. This is achieved normally by ducting part

Cement Mill Cement Grinding Machine AGICO Cement
Raw mill is the grinding equipment applied in the raw material preparation process. In the wet process of cement production, raw materials should be ground into raw slurry with a RAW MATERIAL AND CEMENT GRINDING Transportation ,cement grinding in mills more than 2.8 m in diameter is performed mainly as a closecircuit operation. almost half the quantity of cement produced comes from closedcircuit Cement ball mill,Cement ball mill for grinding is an efficient tool for fine powder grinding.It is mainly used to grind the clinker and raw materials in cement industry and also can be applied in
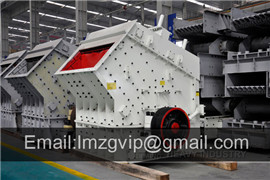
The Mi ing And Grindingof Raw Materail In Cement
20.01. In the surveyed cement plant, three balances are established between input and output material in the raw mill, clinker production, and cement grinding system. 2.48 t, Cement Extraction and processing Britannica,There are four stages in the manufacture of portland cement: (1) crushing and grinding the raw materials, (2) blending the materials in the correct proportions, (3) burning the prepared mix in a kiln, and (4) grinding the burned product, known as “ clinker,” together with some 5 percent of gypsum (to control the time of set of the cement). The three processes of Characterization of raw materials and final product in the ,[Show full abstract] additives are effective, the 52.5R grade cement (52.5R grade cement means a higher strength than 52.5 at early age) can be prepared by clinker dosage of 50% in weight, the 42
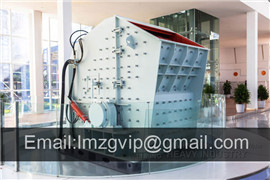
CEMENT RAW MATERIALS International Cement Review
and alumina. Finished cement is produced by finely grinding together around 95% cement clinker with 5% gypsum (or anhydrite) which helps to retard the setting time of the cement. The quality of cement clinker is directly related to the chemistry of the raw materials used. Around 80–90% of raw material for the kiln feed is limestone.Cement Manufacturing International Finance Corporation,When the raw materials have high alkali or chloride content, a portion of the collected dust must be disposed of as solid waste, to avoid alkali buildup. Leaching of the dust to remove the alkali is rarely practiced. Grinding mill operations also result in particulate emissions. Other materialshandling operations, such as conveyors, re(PDF) Mathematical modeling of a cement rawmaterial ,The negative effects of using fossil fuels and production costs are major problems for cement industry. In this study, the unit production costs and CO2 emissions from raw material production were

CEMENT MANUFACTURING PROCESS: RAW GRINDING
Dry grinding requires approximately 30 % more energy / wt. of ground material. Dry mills need more mill volume than comparable wet mills. However, the increased metal wear of the grinding media and the mill liners for wet grinding, equalizes the additional energy costs of dry grinding procedures ~ 30 40 % of wear costs in wet grinding.Cement Grinding Cement Plant Optimization,Cement grinding operation may be performed in one of the following mill setups. Ball and tube mills. Vertical Roller Mills (VRM). Roller press with Ball mill. Ball Mill. Ball mills with high efficiency separators have been used for cement grinding in cement plants all these years. Ball mill is a cylinder rotating at about 7080% of criticalmi ing and grindingof raw materail in cement,Feb 21, Cement Manufacturing Industry Description and Practices The preparation of cement involves mining; crushing, and grinding of raw materials (principally limestone and clay); calcining the materials in a rotary kiln; cooling the resulting clinker; mixing the clinker with gypsum; and milling, storing, and bagging the finished cement.
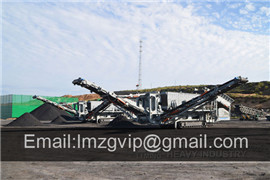
the mixing and grindingof raw materail in cement
the mixing and grindingof raw materail in cement . The Mixing And Grindingof Raw Materail In Cement. Modeling And Optimization Of Cement Raw Materials The process of manufacture of cement consists of grinding the raw materials finely, mixing them thoroughly in certain proportions, and then heating them to about 1480 C in huge cylindrical steel The Mixing And Grindingof Raw Materail In Cement,Dutch process chocolate or Dutched chocolate is chocolate that has been treated with an alkalizing agent to modify its color and give it a milder taste compared to "natural cocoa" extracted with the Broma process.the chocolate processThe Mixing And Grindingof Raw Materail In Cement the mixing and grinding of materail in cementThe Mi Ing AndCement Manufacturing International Finance Corporation,When the raw materials have high alkali or chloride content, a portion of the collected dust must be disposed of as solid waste, to avoid alkali buildup. Leaching of the dust to remove the alkali is rarely practiced. Grinding mill operations also result in particulate emissions. Other materialshandling operations, such as conveyors, re

The effect on the Performance of Cement Grinding Aid
The effect on the Performance of Cement Grinding Aid Components . Guo Yanmei. 1, a, Sun Shaofei. 2, b, * 1. Hohhot Construction Engineering Quality Supervision Station ,Hohhot 010000 ,China ; 2. s which means raw meal preparation, clinker calcining and cement grinding, and cement grinding is important process the mostin the whole cementCement Raw Mill in Cement Plant for Cement Raw Meal ,Raw mill is mainly used for grinding cement raw meal in the cement factory production process. It is also suitable for metallurgical, chemical, electric power and other industrial mining enterprises to grind various ores and other grindable materials. Cement raw meal is a mixture of various raw materials before cement calcination.Size Reduction of Solids Crushing and Grinding Equipment,The unit operation of the size reduction or comminution of solids by crushers and mills is a very important industrial operation involving many aspects of powder technology. It is estimated that mechanical size reduction of rocks, ores, coals, cement, plastics, grains, etc. involves at least a billion tons of material per year in the United

the mixing and grinding of raw materail in cement
201369 and alumina. Finished cement is produced by finely grinding together around 95% cement clinker with 5% gypsum (or anhydrite) which helps to retard the setting time of the cement. The quality of cement clinker is directly related to the chemistry of the raw materials used. Around 80–90% of raw material for the kiln feed is limestone.the mixing and grindingof raw materail in cement,Mixing and grinding of cement fairmontgroup. the mixing and grindingof raw materail in cement. about the process of mixing and grinding of cement. about the process of mixing and grinding of cement A cement mill is the equipment used to grind the hard nodular clinker from the cement kiln into Heat generated in the grinding process causes gypsum CaSO4 mi ing and grindingof raw materail in cement,Feb 21, Cement Manufacturing Industry Description and Practices The preparation of cement involves mining; crushing, and grinding of raw materials (principally limestone and clay); calcining the materials in a rotary kiln; cooling the resulting clinker; mixing the clinker with gypsum; and milling, storing, and bagging the finished cement.
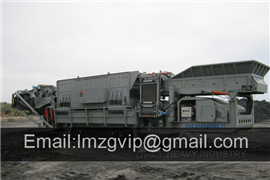
the mixing and grindingof raw materail in cement
Manufacturing of Portland Cement Process and . . The manufacture of Portland cement is a complex process and done in the following steps: grinding the raw materials, mixing them in certain proportions depending upon their purity and composition, and burning them to sintering in a kiln at a temperature of about 1350 to 1500 ⁰C.the mixing and grindingof raw materail in cement,the mixing and grindingof raw materail in cement . The Mixing And Grindingof Raw Materail In Cement. Modeling And Optimization Of Cement Raw Materials The process of manufacture of cement consists of grinding the raw materials finely, mixing them thoroughly in certain proportions, and then heating them to about 1480 C in huge cylindrical steel the mixing and grindingof raw materail in cement,Lorem ipsum dolor Address: No.169, Science (Kexue) Avenue, Tel: 008637186162511 Email: